The logistics and supply chain industry relies heavily on two main types of facilities: fulfillment centers and warehouses. While both are crucial in managing inventory and ensuring product availability, they serve different purposes and operate differently. This article explores fulfillment center vs warehouse differences, including functions, technology, integration, costs, location considerations, labor requirements, customer impact, industry examples, and future trends for both facilities. Understanding these distinctions is vital for effective warehouse network optimization, as it allows businesses to streamline operations and improve overall efficiency.
Fulfillment Center vs Warehouse (Key Differences)
Understanding the core definitions and distinctions between fulfillment centers and warehouses is essential for comprehending their roles in the supply chain.
Fulfillment Center Definition
A fulfillment center is a facility where products are stored, processed, and shipped directly to customers. These centers handle order processing, inventory management, and returns handling. They are integral to the operations of e-commerce businesses, ensuring that customer orders are efficiently processed and delivered. Fulfillment centers are designed to handle high volumes of individual orders, leveraging advanced technology and automation to maintain speed and accuracy.
Warehouse Definition
A warehouse is a large storage facility that stores goods in bulk for extended periods. The primary functions are inventory control, storage, and distribution to various locations. Warehouses support manufacturers, wholesalers, and retailers by maintaining large quantities of products and ensuring a steady supply to fulfillment centers or retail outlets. They focus on long-term storage and efficient handling of bulk goods.
Primary Differences
The primary differences between fulfillment centers and warehouses lie in their purpose and operations. Fulfillment centers are designed for fast order processing and direct shipment to customers, engaging in dynamic activities like picking, packing, and shipping. In contrast, warehouses emphasize long-term storage and bulk inventory management, focusing on receiving, storing, and distributing large quantities of goods.
Purpose and Goals
- Fulfillment Center: Aims to fulfill customer orders and provide quick and efficient delivery.
- Warehouse: Aims to manage inventory and ensure a steady supply of products to retailers or other distribution points.
Functions and Operations
The functions and operations of fulfillment centers and warehouses differ significantly due to their distinct roles in the supply chain.
Order Processing
Fulfillment centers specialize in picking, packing, and shipping individual customer orders. These activities are central to their operation and require meticulous attention to detail and speed. On the other hand, warehouses may handle bulk shipments but usually don’t process individual orders, focusing instead on efficiently handling large volumes of goods.
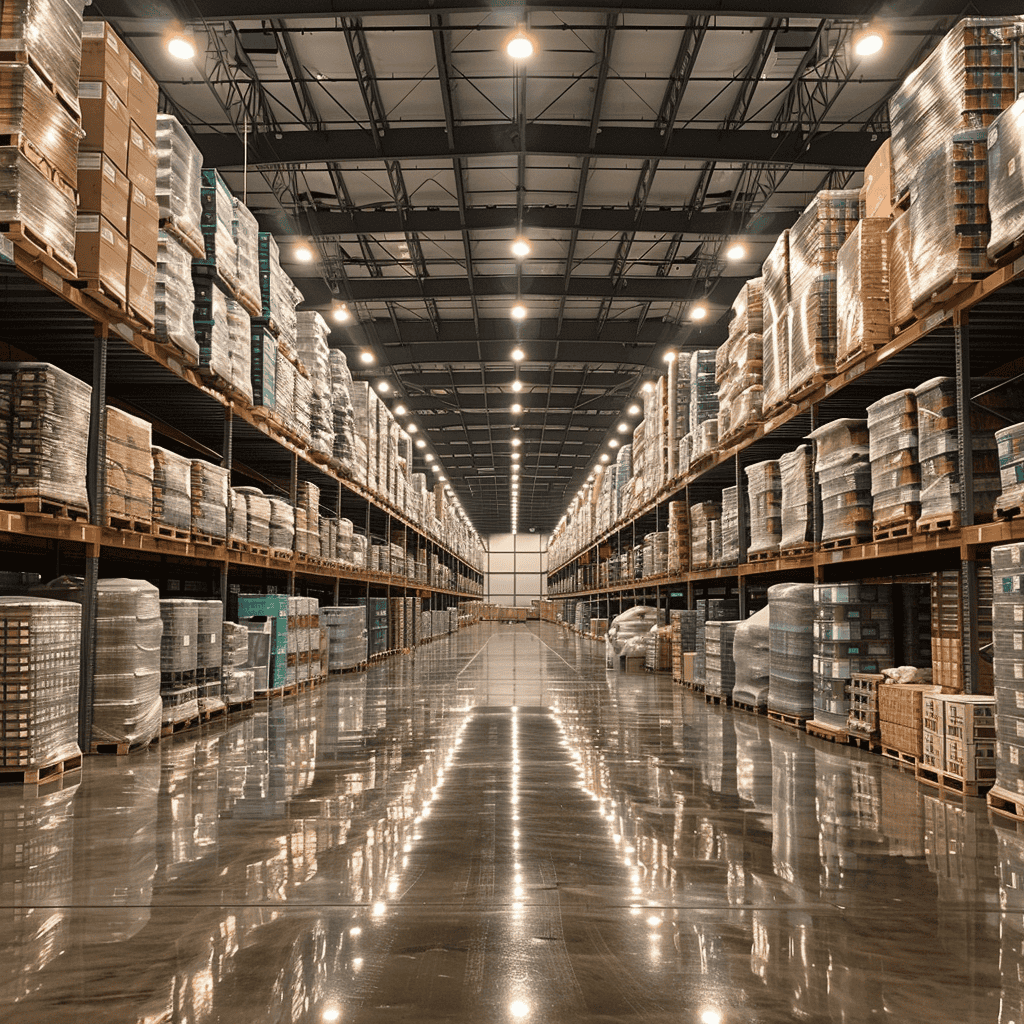
Inventory Management
Both fulfillment centers and warehouses manage inventory, but their approaches differ. Fulfillment centers track real-time stock levels to meet customer demand quickly, employing sophisticated inventory management systems to ensure accuracy. Warehouses focus on maintaining sufficient stock levels for future distribution, often storing goods for longer periods.
Shipping and Receiving
Fulfillment centers handle shipping directly to customers and manage returns, which involves receiving products back, inspecting them, and restocking or disposing them. Warehouses receive bulk goods from manufacturers and ship them to retail locations or fulfillment centers, facilitating the flow of goods through the supply chain.
Returns Handling
Fulfillment centers process returns efficiently, restocking items or handling their disposal. This function is crucial for maintaining customer satisfaction and managing inventory levels. Warehouses typically don’t deal with customer returns directly but may assist in restocking.
Technology and Automation
Technology and automation play vital roles in the efficiency and effectiveness of both fulfillment centers and warehouses.
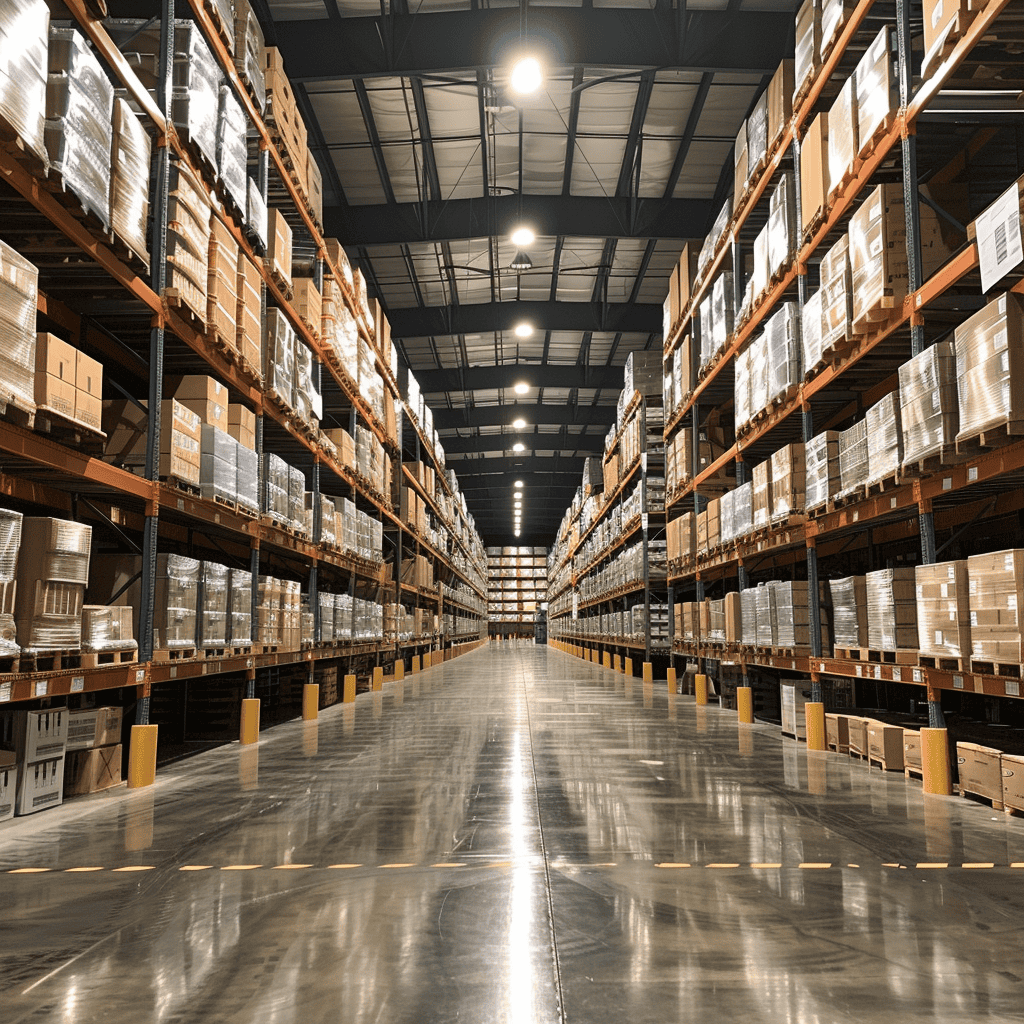
Automation in Fulfillment Centers
Fulfillment centers use advanced automation for picking, packing, and shipping to increase efficiency and speed. Technologies such as conveyor belts, robotic arms, and automated sorting systems streamline these processes, reducing labor costs and improving order accuracy.
Warehouse Management Systems (WMS)
Both fulfillment centers and warehouses use WMS to track inventory, manage storage locations, and streamline operations. However, the systems in fulfillment centers often integrate more closely with order management systems to ensure seamless processing from order receipt to delivery.
Robotics and AI
Fulfillment centers increasingly use robotics and AI for sorting, packing, and inventory management tasks. These technologies enhance efficiency, reduce human error, and enable the centers to handle high orders. Warehouses also use these technologies, but primarily for handling large quantities of goods, such as palletizing and depalletizing.
Inventory Tracking Technologies
Both types of facilities use barcodes, RFID, and other tracking technologies. Fulfillment centers need real-time tracking to manage fast-moving inventory and ensure order accuracy, while warehouses focus on maintaining accurate records of stored goods and their locations.
Supply Chain Integration
The integration of fulfillment centers and warehouses into the supply chain is crucial for the smooth operation of logistics and inventory management.
Role in Supply Chain
Fulfillment centers are the final link in the supply chain, directly interfacing with customers. They are responsible for ensuring that orders are processed and delivered promptly. Warehouses serve as intermediaries, storing goods before they reach fulfillment centers or retail stores, and ensuring that there is a steady supply of products.
Logistics Coordination
Fulfillment centers coordinate logistics to ensure timely delivery to customers. This involves managing carrier relationships, optimizing shipping routes, and tracking deliveries. Warehouses manage logistics to ensure a steady supply to distribution points, coordinating with manufacturers and transport providers.
Vendor Relationships
Fulfillment centers often work closely with e-commerce vendors to manage inventory and orders. This collaboration ensures that stock levels are maintained and customer orders are fulfilled efficiently. Warehouses maintain relationships with manufacturers and distributors, focusing on the efficient storage and bulk handling of goods.
Customer Order Flow
Fulfillment centers handle customer orders from receipt to delivery, ensuring a smooth and efficient process. This includes managing order peaks during busy periods. Warehouses support this flow by supplying products to fulfillment centers, ensuring that there is always enough inventory to meet demand.
Cost Considerations
Understanding the cost dynamics of fulfillment centers and warehouses is essential for effective financial planning and operational efficiency.
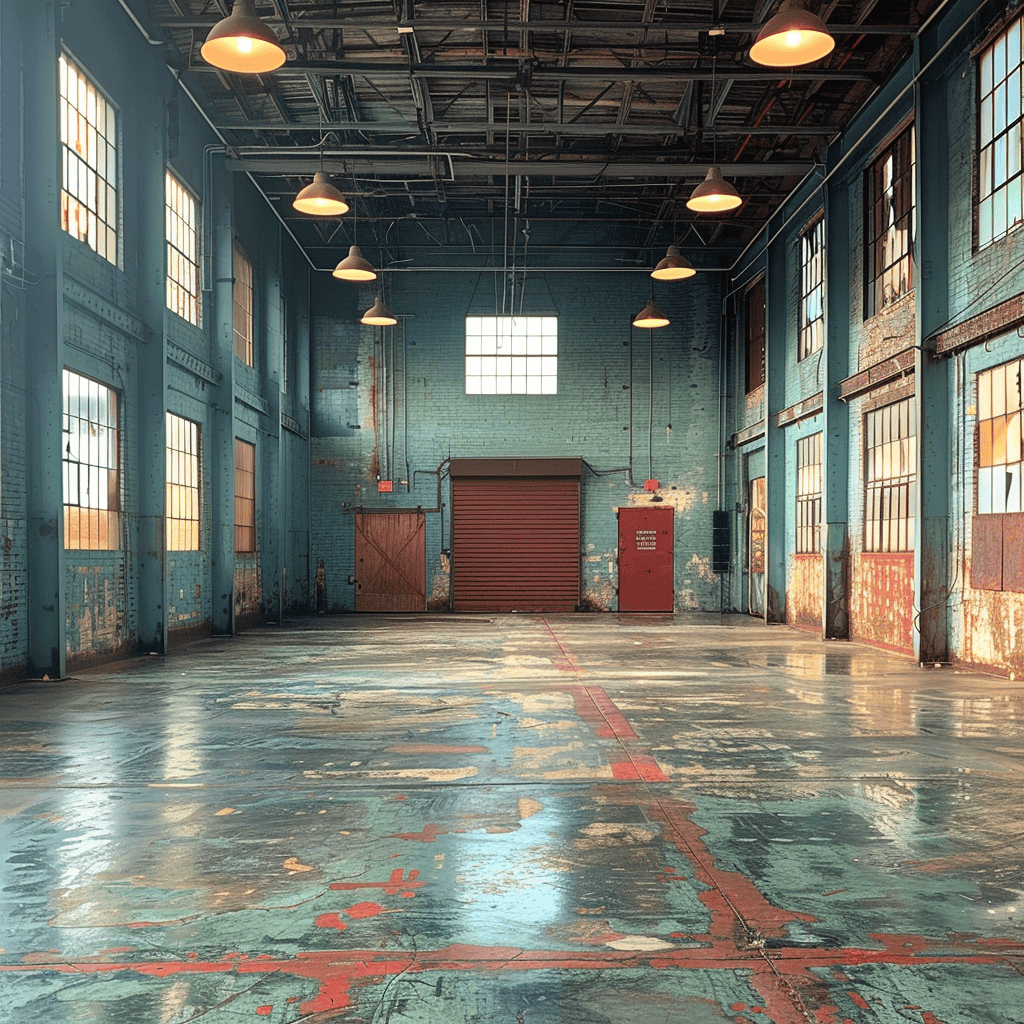
Operational Costs
Fulfillment centers have higher operational costs due to advanced technology and labor-intensive processes. The benefits of faster order processing and improved customer satisfaction offset these costs. Warehouses have lower operational costs, focusing on efficient storage and handling of bulk goods.
Technology Investment
Fulfillment centers invest heavily in automation and real-time inventory tracking technologies to enhance efficiency and accuracy. Warehouses invest in storage and inventory management systems, but their technology needs are generally less sophisticated.
Labor Costs
Labor costs are higher in fulfillment centers due to the need for skilled workers to process orders and operate advanced technologies. Warehouses require fewer skilled workers, and labor costs are focused on tasks such as inventory control and bulk handling.
Cost-Benefit Analysis
The benefits of faster delivery and better customer satisfaction justify the higher costs of fulfillment centers. Warehouses benefit from economies of scale in storage, reducing per-unit storage costs and ensuring a steady supply of products.
Location and Size
The strategic location and size of fulfillment centers and warehouses significantly impact their efficiency and effectiveness.
Strategic Location Choices
Fulfillment centers are strategically located near major markets to ensure quick customer delivery. This proximity reduces shipping times and costs. To facilitate efficient distribution, warehouses are often located near transportation hubs, such as ports, railways, and highways.
Facility Size and Layout
Fulfillment centers are smaller with layouts designed for fast order processing and high inventory turnover. Warehouses are larger, with layouts optimized for bulk storage and efficient handling of large volumes of goods.
Proximity to Markets
Fulfillment centers are close to end markets to provide quick delivery. This strategic positioning is crucial for meeting customer expectations for fast shipping. Warehouses are close to manufacturing sites or major transit routes, ensuring efficient movement of goods through the supply chain.
Real Estate Considerations
Fulfillment centers require premium real estate near urban areas, which can be costly but is necessary for quick delivery times. Warehouses can be located in less expensive, rural or industrial areas, reducing real estate costs while providing ample space for bulk storage.
Labor and Workforce
The labor and workforce requirements of fulfillment centers and warehouses differ due to their distinct operational needs.
Workforce Requirements
Fulfillment centers need a workforce skilled in order processing, technology use, and customer service. These workers are crucial for maintaining the high efficiency and accuracy required in fulfillment operations. Warehouses need workers for inventory management and bulk handling, focusing on the physical aspects of storing and moving large quantities of goods.
Training and Skills
Fulfillment center workers need training in using automation and technology, such as warehouse management systems and robotic equipment. They also require skills in order accuracy and customer service. Warehouse workers need skills in inventory control, equipment operation, and safety procedures, ensuring efficient and safe handling of bulk goods.
Labor Challenges
Fulfillment centers face challenges in finding skilled labor and managing high turnover rates due to the demanding nature of the work. Warehouses deal with the physical demands of bulk handling and storage, requiring workers to be trained in proper lifting techniques and safety practices to prevent injuries.
Safety and Working Conditions
Both fulfillment centers and warehouses prioritize safety, but fulfillment centers have additional considerations due to the fast-paced environment and use of automation. Warehouses focus on ensuring safe storage practices and handling of bulk goods, with emphasis on preventing accidents and maintaining a safe working environment.
Customer Impact
The operations of fulfillment centers and warehouses directly impact customer satisfaction and overall service quality.
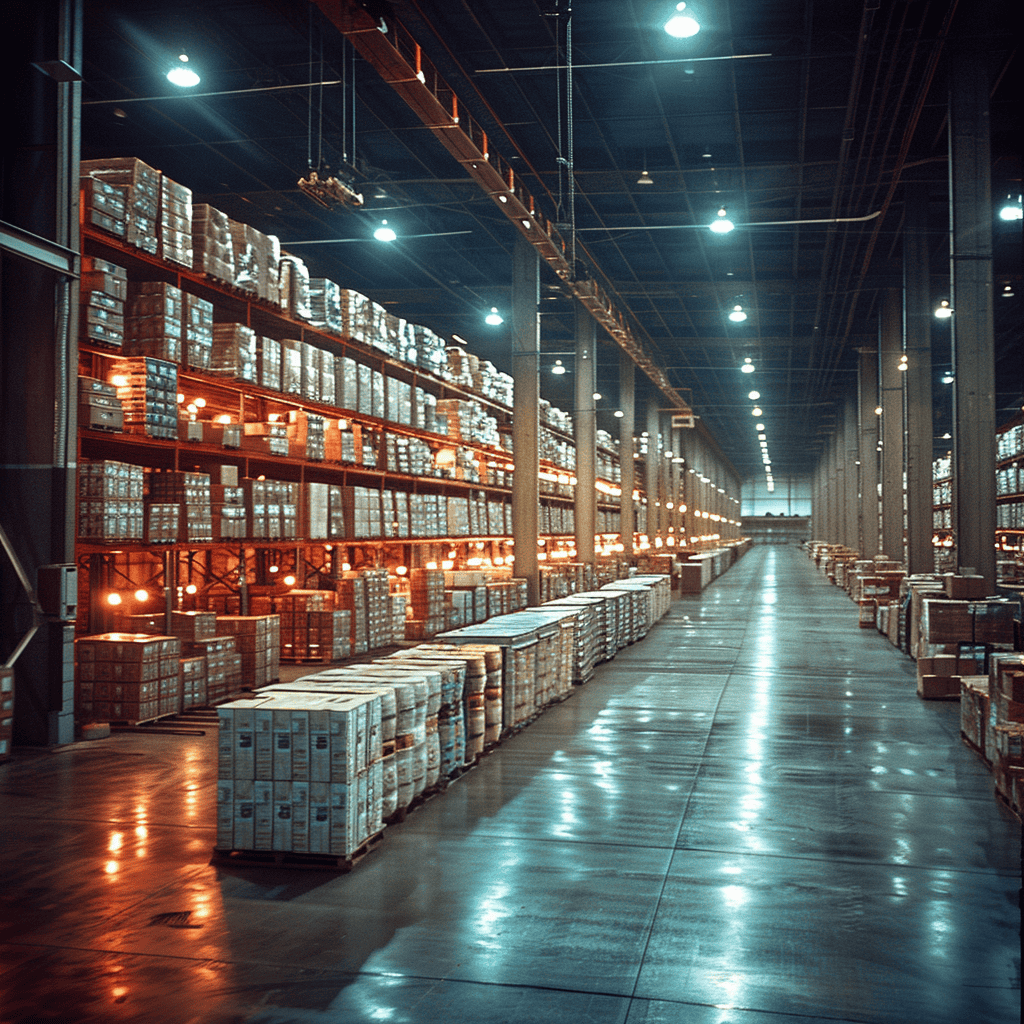
Service Speed
Fulfillment centers provide fast delivery directly to customers, meeting the high expectations of e-commerce shoppers. Warehouses impact delivery speed by ensuring a steady supply to fulfillment centers, which then process and ship orders quickly.
Order Accuracy
Fulfillment centers focus on high order accuracy to meet customer expectations. Advanced technologies and meticulous processes ensure that orders are fulfilled correctly. Warehouses ensure accuracy in bulk shipments to prevent supply chain disruptions and ensure that fulfillment centers receive the correct products.
Customer Satisfaction
Fulfillment centers directly influence customer satisfaction through fast delivery and accurate orders. Efficient operations and quick handling of returns contribute to a positive customer experience. Warehouses support this by maintaining reliable inventory levels and ensuring that fulfillment centers are well-stocked.
Return Policies
Fulfillment centers handle customer returns efficiently, impacting overall customer satisfaction. They process returns, restock items, or handle their disposal as necessary. Warehouses support return processes by restocking or redistributing returned goods, ensuring inventory levels are maintained.
Industry Examples
Examples of fulfillment centers and warehouses in various industries highlight their importance and distinct roles.
Amazon Fulfillment Centers
Amazon’s network of fulfillment centers exemplifies the advanced use of automation and efficient order processing to meet global demand. These centers handle millions of orders daily, employing sophisticated technologies and streamlined processes to ensure quick and accurate delivery.
Retail Warehouses
Large retailers store inventory in warehouses before distributing it to individual stores, ensuring they can meet customer demand. These warehouses manage bulk inventory, ensuring that products are available when needed and supporting the operations of retail outlets.
Third-Party Logistics Providers (3PL)
3PLs offer fulfillment and warehousing services, providing flexible solutions for businesses of all sizes. They manage inventory, process orders, and handle shipping and returns, allowing companies to outsource their logistics needs and focus on core operations.
E-commerce vs. Traditional Retail
E-commerce relies heavily on fulfillment centers for direct-to-customer delivery, ensuring quick and accurate order processing. Traditional retail uses warehouses to supply physical stores, maintaining inventory levels and ensuring products are available for in-store shoppers.
Future Trends and Innovations
Emerging trends and innovations will shape the future of fulfillment centers and warehouses, driving improvements in efficiency and sustainability.
Emerging Technologies
Fulfillment centers and warehouses will continue adopting advanced technologies like AI, robotics, and IoT for improved efficiency and accuracy. These technologies will enhance automation, reduce labor costs, and improve inventory management, ensuring operations remain competitive.
Sustainability Practices
Sustainability will become increasingly important, with both types of facilities adopting eco-friendly practices and reducing carbon footprints. This includes using energy-efficient equipment, optimizing transportation routes, and implementing recycling and waste reduction programs.
Evolving Customer Expectations
Customer expectations for faster delivery and higher accuracy will drive innovations in fulfillment centers. Warehouses must support these demands by improving inventory management and logistics coordination, ensuring that fulfillment centers can effectively meet customer needs.
Global Expansion
As businesses expand globally, fulfillment centers and warehouses must adapt to new markets and regulatory environments, requiring flexibility and strategic planning. This includes establishing facilities in new regions, complying with local regulations, and managing cross-border logistics efficiently.