When deciding on a warehousing strategy, companies must evaluate their needs, budget, and long-term goals. Dedicated and shared warehousing are two primary options, each with unique benefits and drawbacks. This comprehensive analysis will explore both types in detail to help businesses make informed decisions.
Dedicated Warehousing Versus Shared Warehousing
Here is a detailed comparison of Dedicated Warehousing Versus Shared Warehousing:
1. Dedicated Warehousing
Definition: Dedicated warehousing, also known as exclusive warehousing, involves a company leasing or owning a warehouse space exclusively for its own use. This approach offers complete control over the facility and operations.
Key Features:
- Control and Customization: Companies have full control over the warehouse environment, allowing for implementing specific layouts, technology, and processes that cater to their unique requirements.
- Branding: The warehouse can be customized and branded to reflect the company’s identity, enhancing corporate image and consistency.
- Consistency: The warehouse staff and resources are dedicated solely to the company’s operations, ensuring uniformity in service levels.
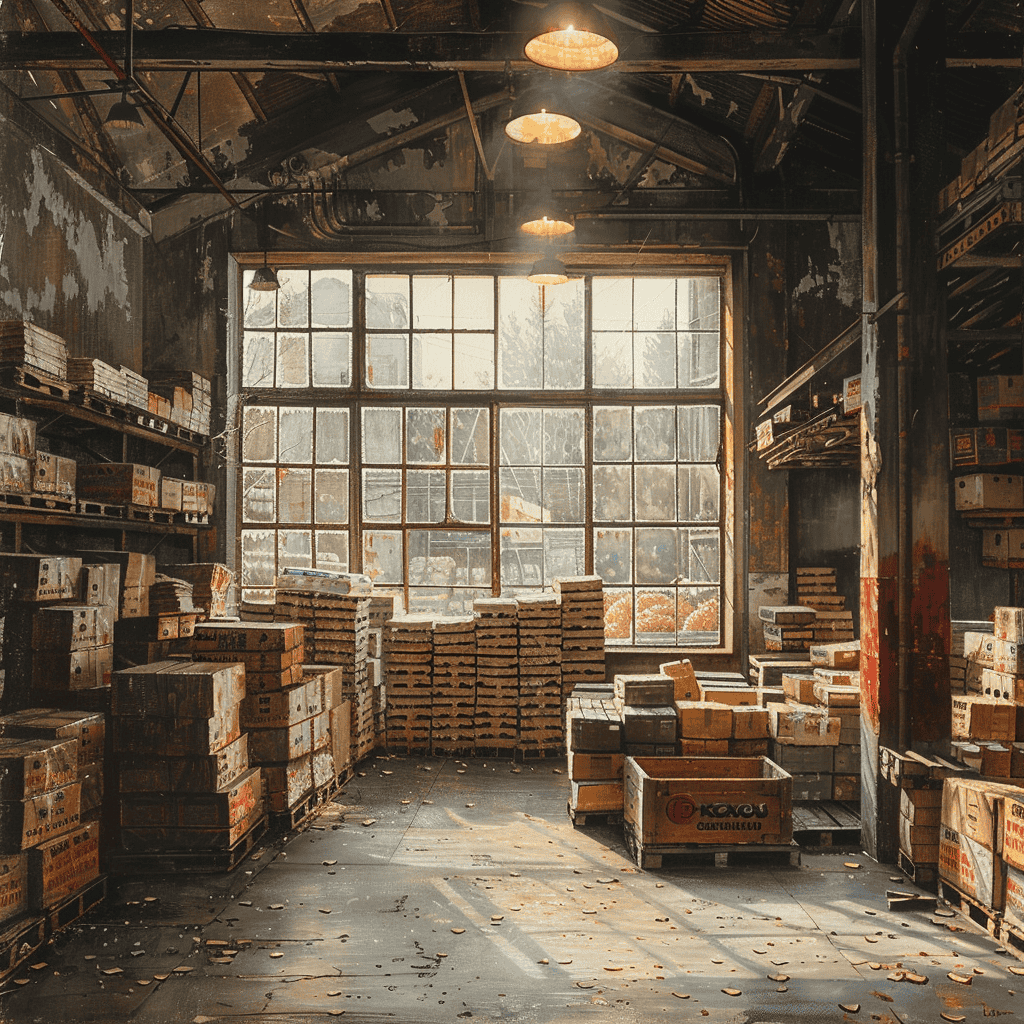
Advantages:
- Operational Control: Full control over inventory management, order fulfillment processes, and operational procedures allows companies to optimize efficiency and effectiveness.
- Security: Higher levels of security since access is restricted to the company’s personnel and authorized visitors, reducing the risk of theft or mishandling.
- Customization: Ability to integrate specialized equipment, technology, and workflows tailored to specific business needs, such as temperature-controlled storage or automated systems.
Disadvantages:
- Cost: There are higher operational and capital expenses due to the need to cover the full cost of the warehouse, including rent, utilities, staffing, and maintenance. Initial setup costs can be substantial.
- Scalability: Less flexibility to adjust to fluctuations in demand. Companies might face underutilization during off-peak periods or struggle to expand quickly during peak times.
- Complexity: Increased complexity in managing warehouse operations independently, requiring substantial expertise and resources.
2. Shared Warehousing
Definition: Shared warehousing, or public warehousing, involves utilizing a third-party logistics provider (3PL) that manages a warehouse space shared by multiple clients. This model allows companies to benefit from shared resources and costs.
Key Features:
- Shared Resources: Multiple companies share the warehouse space, staff, and equipment, leading to cost savings through economies of scale.
- Flexibility: This allows you to scale space and resources up or down based on seasonal or fluctuating demand without long-term commitments.
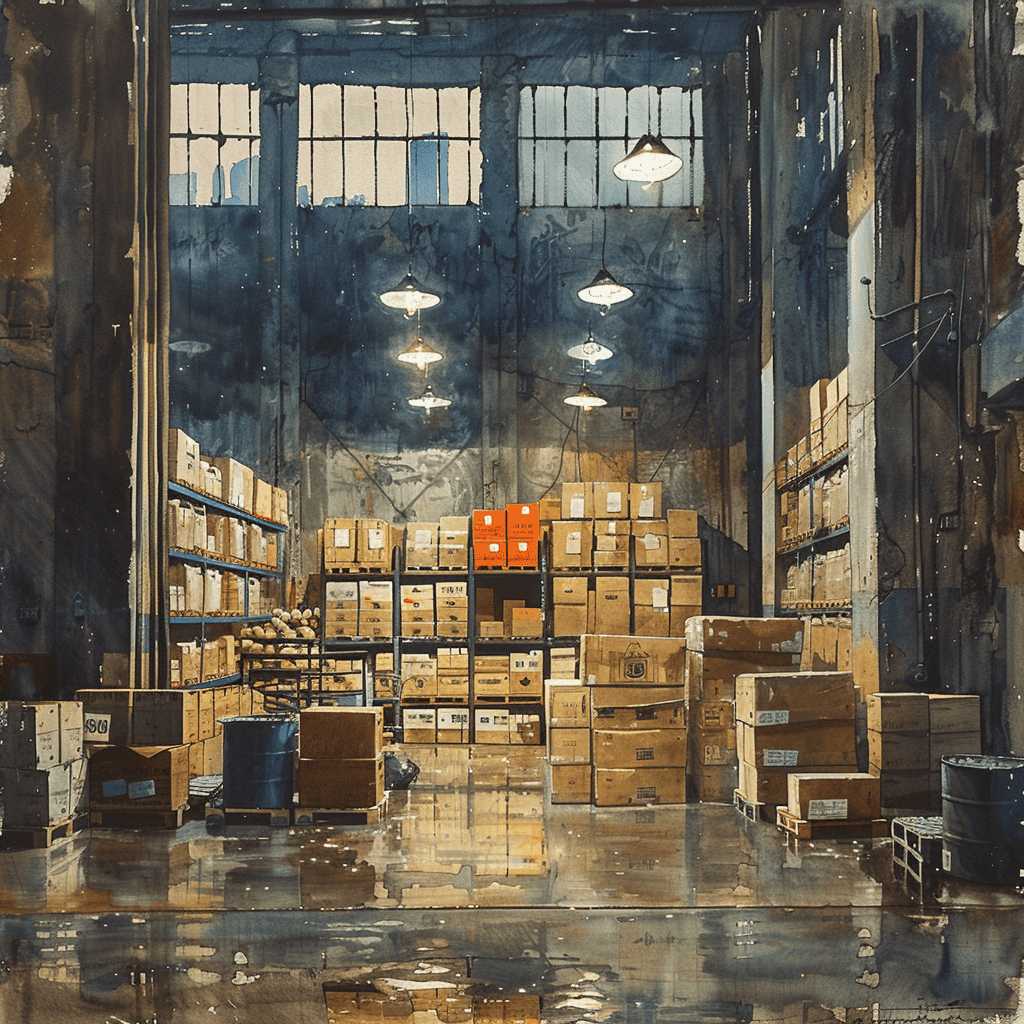
Advantages:
- Cost Efficiency: Lower costs due to shared resources. Companies pay only for the space and services they use, avoiding the high capital expenditure of dedicated facilities.
- Scalability: High flexibility to scale operations in response to market demands without the need for significant capital investment. Easy to adjust warehouse space and services based on business growth or seasonal peaks.
- Expertise: Access to the 3PL’s warehouse management, logistics, and technology expertise. This can improve efficiency and reduce the company’s internal resources burden.
- Speed to Market: Faster setup times compared to establishing a dedicated warehouse, enabling quicker market entry or response to demand changes.
Disadvantages:
- Less Control: Limited control over warehouse operations, processes, and systems, which might not be fully aligned with the company’s specific needs.
- Potential Delays: Due to shared resources, there may be delays in order processing and fulfillment, especially during peak periods when multiple clients compete for the same services.
- Branding and Customization: There are limited opportunities for branding and customization within the shared space. Standardized processes may not align with all specific business requirements.
Comparison Factors
Cost:
- Dedicated: Higher due to exclusive use and full operational responsibilities, including fixed costs like rent, utilities, and labor.
- Shared: Lower due to cost-sharing among multiple clients. Variable costs are based on usage, providing better cost management and predictability.
Control:
- Dedicated: Full control over operations, security measures, inventory systems, and customization options.
- Shared: Limited control as the 3PL manages operations. Clients must adapt to standardized procedures and protocols.
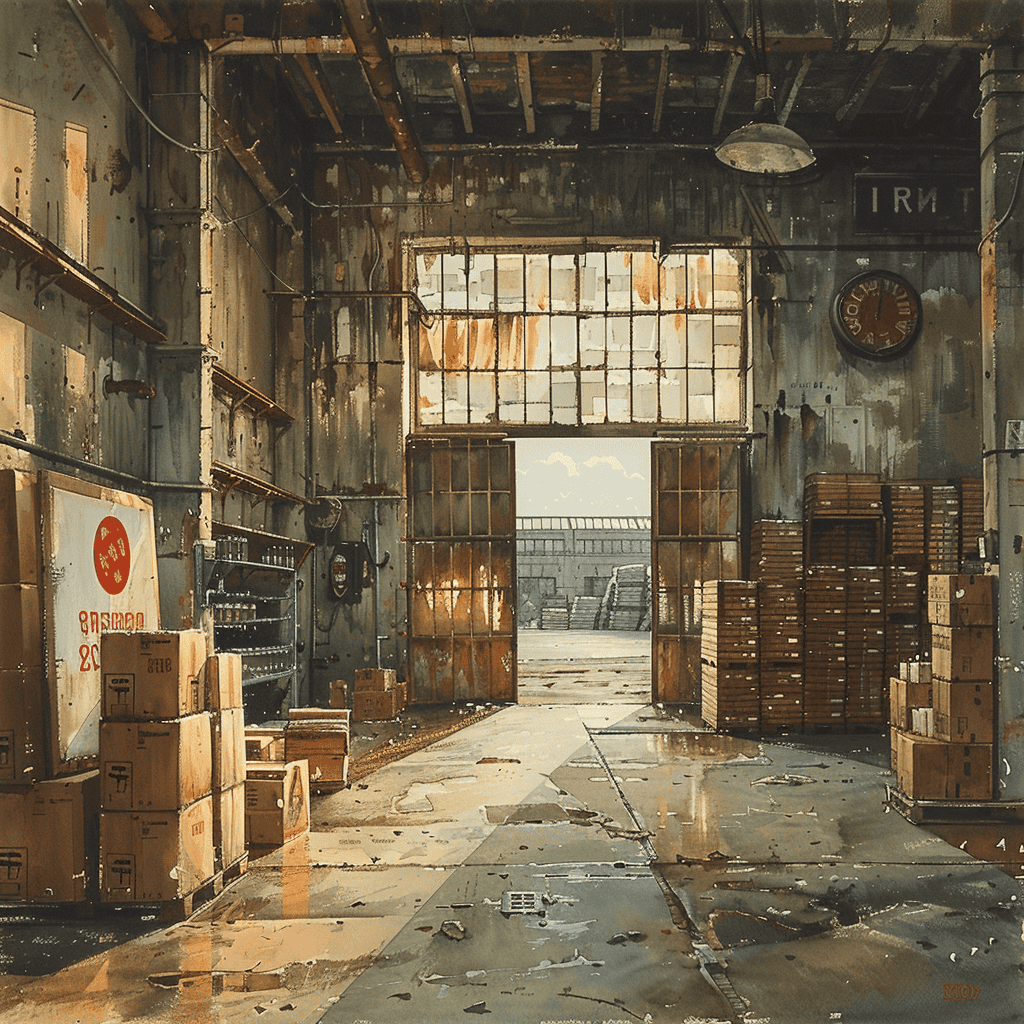
Scalability:
- Dedicated: Less flexible, may face challenges with underutilization during off-peak times or capacity constraints during peak periods.
- Shared: Highly flexible, easily adjustable based on demand without the need for long-term commitments.
Operational Complexity:
- Dedicated: Higher complexity, requiring in-house management expertise and resources to handle all aspects of warehouse operations.
- Shared: Lower complexity for the client, as the 3PL handles operational tasks, allowing the client to focus on core business activities.
Risk:
- Dedicated: Higher financial risk due to significant upfront investment and ongoing operational costs.
- Shared: Lower financial risk with shared costs and flexible terms. Easier to adjust spending based on business performance and market conditions.
Strategic Considerations
When deciding between dedicated and shared warehousing, companies should consider the following strategic factors:
- Business Size and Growth Stage:
- Startups and Small Businesses: Often benefit from shared warehousing due to lower costs and flexibility.
- Established Companies: May prefer dedicated warehousing for greater control and customization.
- Product Type and Requirements:
- Specialized Products: Products requiring specific storage conditions (e.g., pharmaceuticals, perishable goods) may necessitate dedicated warehousing.
- Standard Products: General consumer goods can often be accommodated in shared warehousing environments.
- Volume and Seasonality:
- High Volume: Companies with consistent high-volume throughput may find dedicated warehousing more cost-effective in the long run.
- Seasonal Demand: Businesses with significant seasonal fluctuations benefit from the scalability of shared warehousing.
- Logistics Strategy:
- Centralized Logistics: Companies with a centralized logistics strategy might prefer dedicated warehousing to centralize control.
- Decentralized Logistics: Companies using a decentralized approach can leverage multiple shared warehousing locations for broader reach and flexibility.
Conclusion
The choice between dedicated and shared warehousing hinges on a company’s specific needs, operational priorities, and financial considerations. Dedicated warehousing offers unparalleled control, security, and customization but comes with higher costs and complexity. Shared warehousing provides cost efficiency, flexibility, and professional management at the expense of control and customization.