Just-in-Time (JIT) inventory has been used by many companies over the years, and it has proven to be an effective approach to managing material flow and warehousing operations. But what is JIT inventory and how can it be implemented to support Lean warehousing? In this article, you will learn about implementing Just-in-Time Inventory to streamline operations and enhance efficiency in your warehousing practices.
What is Just-in-Time Inventory?
Just-in-time inventory, or JIT inventory, is an inventory management system that works to minimize waste and maintain the highest quality of service. It is based on the principles of “lean manufacturing” and aims to reduce the amount of materials and supplies stored in warehouses. This system is designed to reduce the amount of time and resources wasted when managing and storing inventory, as well as reducing the amount of money spent on inventory management.
JIT inventory is different from traditional inventory management systems in that it emphasizes the need for a steady stream of materials and supplies rather than large stockpiles of inventory. This system works by scheduling deliveries of materials and supplies at regular intervals.
How Can Material Flow Evaluations Help?
Material flow evaluations can help companies evaluate their current inventory management system and identify areas for improvement. By assessing the current inventory system and operations, companies can identify processes and procedures that can be improved to reduce waste and improve efficiency. For example, companies may find that they are overstocking certain materials and supplies, which can be identified through a material flow evaluation.
Material flow evaluations can also help companies identify the most efficient and cost-effective ways to order and store materials and supplies. Companies can use the evaluations to determine the best times to order materials and supplies and how to store them to maximize efficiency and reduce waste.
Implementing Just-in-Time Inventory Management
Once the material flow evaluation is complete, companies can begin the process of implementing JIT inventory management. Companies should start by assessing their current inventory system and identifying areas for improvement. This could include reducing the amount of time and resources wasted when managing and storing inventory, as well as reducing the amount of money spent on inventory management.
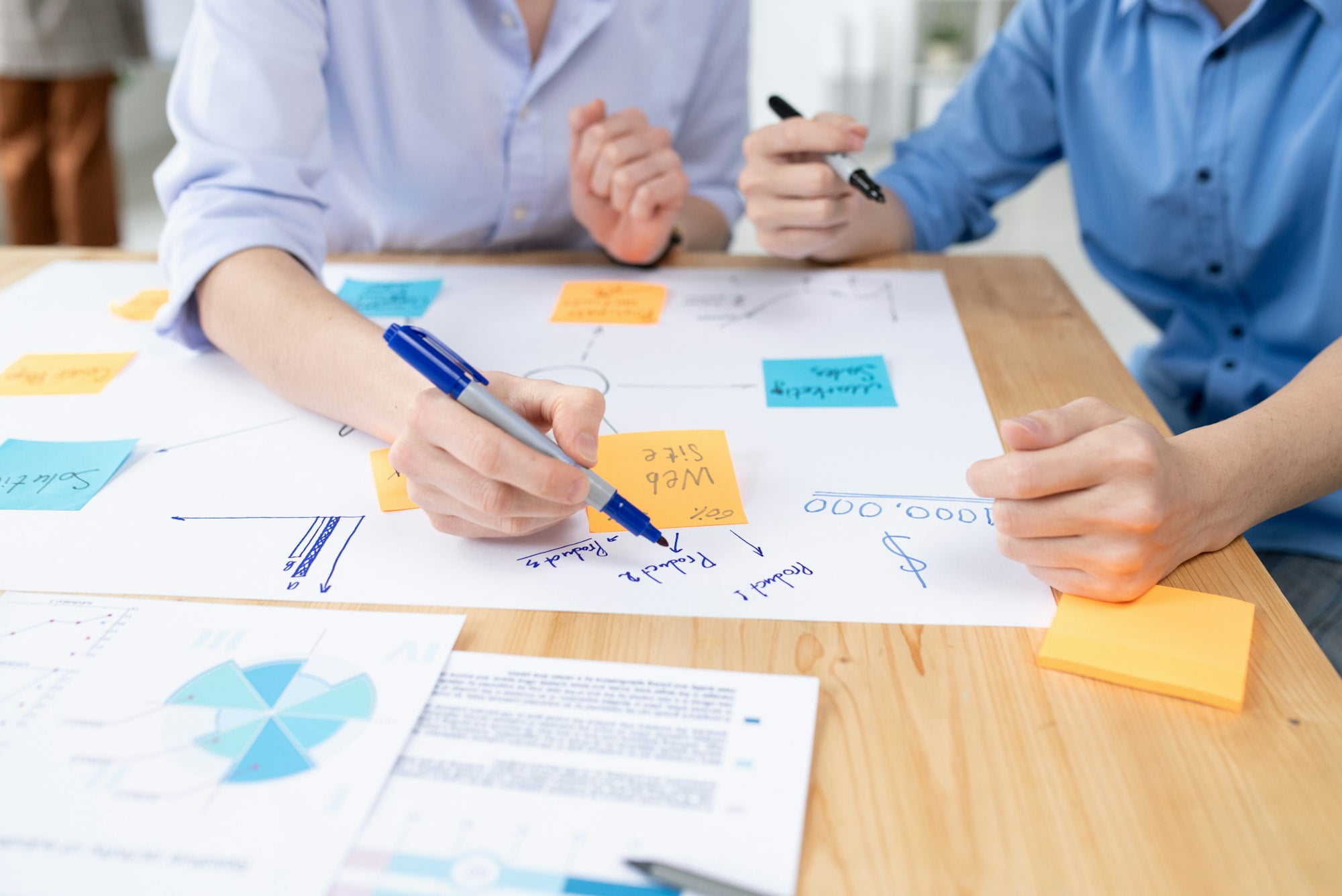
Discussing product implementation
The next step is to identify the best times to order materials and supplies and how to store them in order to maximize efficiency and reduce waste. Companies should also review their current inventory systems and procedures to ensure that they are in line with JIT principles.
Using Material Flow Evaluations To Support Lean Warehousing
Material flow evaluations can help companies implement Lean warehousing operations by identifying areas for improvement in their current warehousing operations. Companies can use the evaluations to identify ways to reduce waste and optimize their warehousing operations.
For example, companies may find that they are overstocking certain materials and supplies, which can be identified through a material flow evaluation.
Challenges and Solutions for JIT Implementation
Transitioning to a Just-in-Time (JIT) inventory system poses unique challenges, ranging from supplier reliability to internal process adjustments. This section delves into the most common obstacles businesses encounter and provides practical solutions backed by case studies. Understanding these challenges and their resolutions can pave the way for smoother JIT implementation and enhanced supply chain efficiency.
Integrating Technology with JIT Systems
Modern technology plays a pivotal role in optimizing JIT inventory systems. This section explores the integration of advanced technologies such as RFID tracking, IoT devices, and sophisticated warehouse management software.
Impact of JIT on Supply Chain Relationships
Implementing JIT inventory management significantly affects relationships with suppliers and logistics partners.
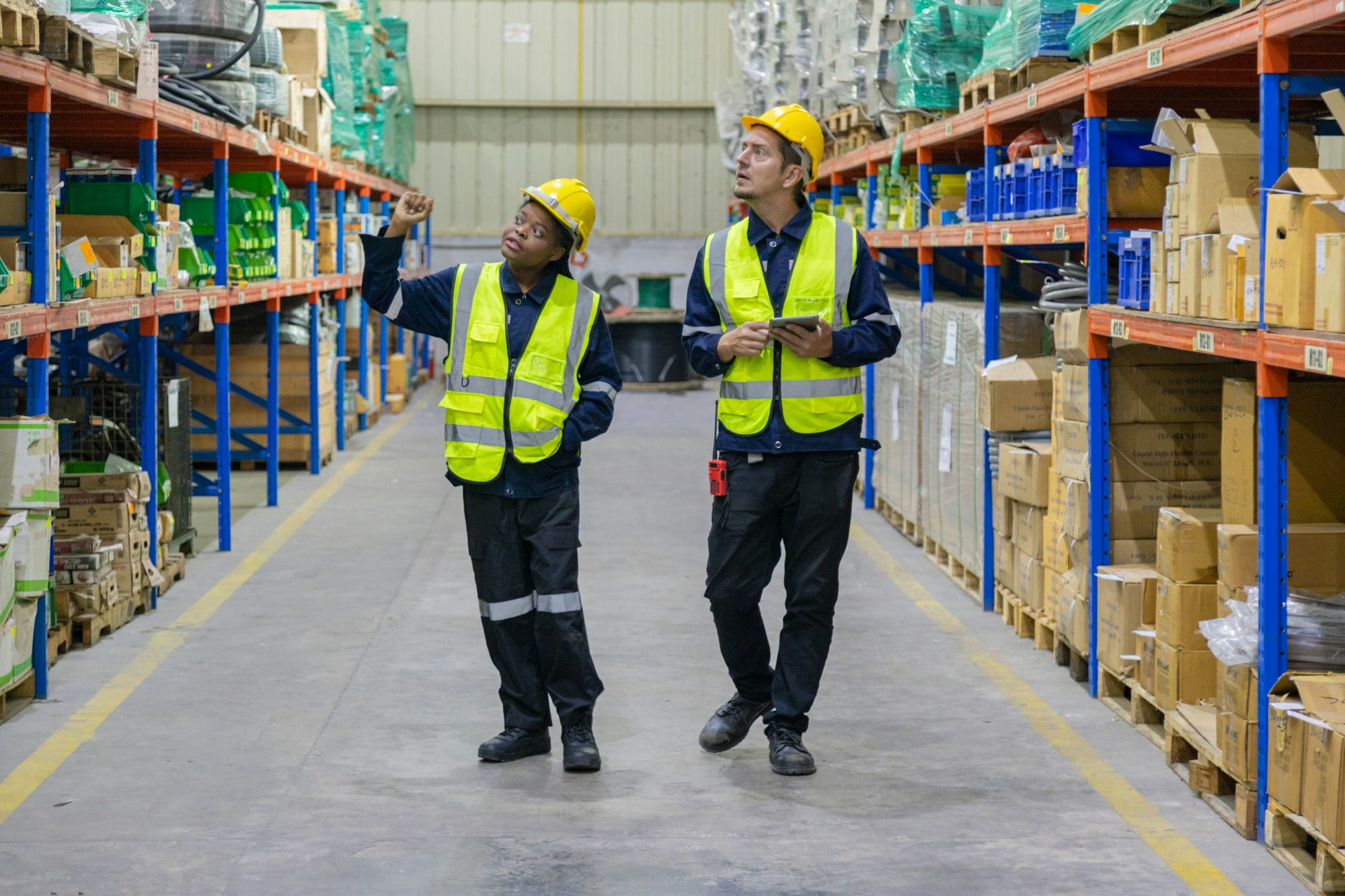
Store clerks inspect products, warehouses, industrial and logistics supply chains.
In this part, we examine how JIT practices demand closer collaboration and communication, the shifts needed to foster these partnerships, and how to manage the dynamics of supply chain relationships to ensure a steady flow of materials.
Evaluating Warehouse Layout for JIT Compatibility
The physical layout of a warehouse greatly influences the effectiveness of JIT systems. This section focuses on evaluating and redesigning warehouse layouts to align with JIT principles, optimizing space utilization, and ensuring that materials flow smoothly and efficiently from receiving to shipping.
Conclusion
By utilizing material flow evaluations, companies can ensure that their Lean warehousing operations are running smoothly and efficiently. This will help them to reduce waste, save money, and maximize efficiency. Ultimately, material flow evaluations can help companies to make the most of their Lean warehousing operations.
By understanding the basics of JIT inventory and utilizing material flow evaluations, companies can ensure that their Lean warehousing operations are running smoothly and efficiently. By reducing waste, saving money, and maximizing efficiency, companies can make the most of their Lean warehousing operations. Material flow evaluations are an important tool for companies looking to make the most of their Lean warehousing operations.