In today’s fast-paced and highly competitive market, efficient warehouse operations are crucial for businesses aiming to meet customer demands and maintain a competitive edge. Accelerating material flow within a warehouse is a key factor in improving overall productivity, reducing operational costs, and enhancing customer satisfaction. This comprehensive guide explores various strategies to optimize warehouse processes, from layout design and inventory management to automation and employee training.
By implementing these strategies, businesses can streamline their warehouse operations, ensuring quicker turnaround times and more efficient material handling. Whether you’re managing a small warehouse or a large distribution center, these insights will help you enhance your warehouse’s efficiency and effectiveness.
Strategies for Accelerating Material Flow in Your Warehouse
Here are some strategies for accelerating material flow in your warehouse:
1. Warehouse Layout Optimization
Design Efficient Layouts
The design of your warehouse layout is crucial for streamlining material flow. Begin by analyzing the frequency of item movements. High-turnover items should be placed closest to shipping and receiving areas to minimize travel time. Use tools like heat maps to understand traffic patterns and identify bottlenecks. Efficiently arranging items based on their picking frequency can drastically reduce travel distances for employees, thereby speeding up the overall process.
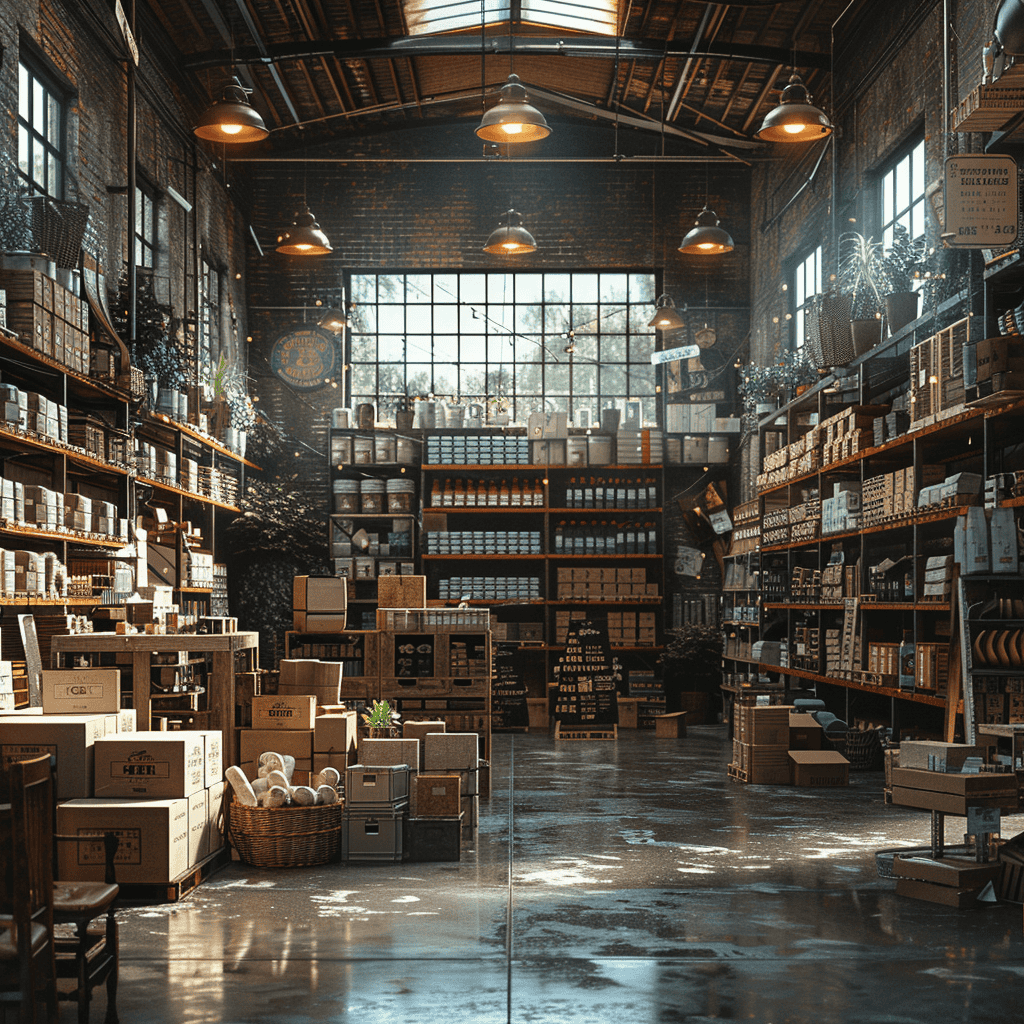
Minimize Aisle Width
While ensuring safety and maneuverability for warehouse equipment, minimizing aisle width can significantly increase storage capacity. Narrow aisles mean more rows of shelving, which can reduce the distance that workers need to travel. However, it’s essential to strike a balance to prevent congestion and ensure that forklifts and other equipment can still operate efficiently.
2. Inventory Management Systems
Implement WMS (Warehouse Management System)
A robust Warehouse Management System (WMS) can automate and optimize various warehouse operations, from inventory tracking to order fulfillment. By providing real-time visibility into inventory levels, a WMS can help in accurately forecasting demand and reducing stockouts or overstock situations. Automation through a WMS can also reduce manual errors and speed up the processes of picking, packing, and shipping.
Use Barcode/RFID Technology
Integrating barcode scanners and RFID tags can enhance accuracy and speed in inventory management. Barcodes and RFID tags allow for quick scanning of items, which updates inventory levels in real-time and reduces the chances of human error. This technology can streamline the picking process, making it faster and more reliable, and can also aid in tracking the movement of goods throughout the warehouse.
3. Automation and Robotics
Automated Guided Vehicles (AGVs)
AGVs can transport goods autonomously within the warehouse, reducing the need for manual labor and minimizing delays. These vehicles follow predetermined paths and can navigate around obstacles, ensuring continuous movement of materials. AGVs can be particularly useful in repetitive tasks such as transporting goods from receiving areas to storage locations.
Conveyor Systems
Conveyor belts can significantly speed up the internal movement of goods. By automating the transport of items between different zones of the warehouse, conveyors can reduce the time workers spend walking and carrying items. This system can be customized to handle different types and sizes of goods, making it versatile and efficient for various warehouse operations.
Robotic Picking Systems
Advanced robotic systems can handle picking and packing tasks with high accuracy and speed. These robots use sophisticated algorithms and machine vision to identify and pick items from shelves. Implementing robotic pickers can not only accelerate the order fulfillment process but also reduce the risk of errors and improve the overall efficiency of the warehouse.
4. Order Picking Optimization
Zone Picking
By dividing the warehouse into distinct zones and assigning specific pickers to each zone, you can minimize the distance that workers need to travel. This approach helps in reducing bottlenecks and ensures that multiple orders can be picked simultaneously, thus speeding up the overall picking process.
Batch Picking
Batch picking involves grouping multiple orders into a single pick run. This method reduces the number of trips pickers need to make, thereby saving time and effort. Batch picking can be particularly effective in environments where multiple orders contain similar items.
Wave Picking
Wave picking organizes the picking schedule into waves based on order priorities and shipping deadlines. By coordinating the picking process with shipping schedules, wave picking ensures that orders are fulfilled efficiently and shipped out on time, improving customer satisfaction.
5. Lean Warehouse Practices
5S Methodology
The 5S methodology (Sort, Set in order, Shine, Standardize, Sustain) is a lean management practice aimed at creating and maintaining an organized, clean, and efficient workspace. By regularly sorting through items, organizing tools and equipment, and maintaining cleanliness, warehouses can reduce clutter and improve workflow, leading to faster material handling and reduced errors.
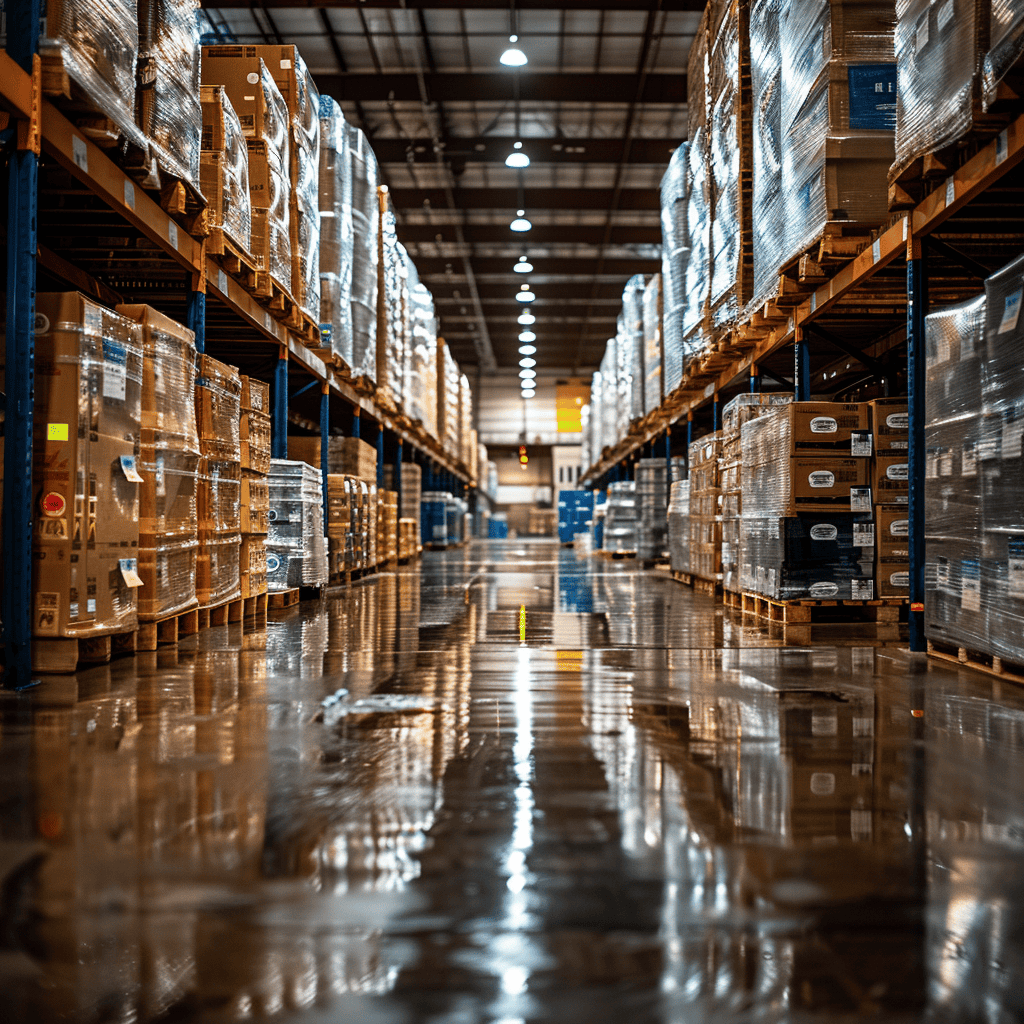
Kaizen
Kaizen, meaning continuous improvement, involves regularly seeking and implementing incremental process improvements. By encouraging employees to suggest and test improvements, warehouses can continuously refine their operations. This proactive approach helps identify inefficiencies and implement solutions that enhance material flow and overall productivity.
6. Employee Training and Productivity
Regular Training Programs
Ongoing training is essential to keep employees updated on the latest technologies, safety protocols, and best practices. Well-trained employees can operate more efficiently and handle materials with greater care, reducing errors and speeding up processes. Training programs should include hands-on practice and refresher courses to keep skills sharp.
Incentive Programs
Implementing incentive programs can motivate employees to achieve higher productivity levels. Rewards for meeting performance targets can drive workers to improve their efficiency and accuracy. Incentives can include monetary bonuses, recognition programs, and other benefits encouraging employees to excel.
7. Real-Time Data and Analytics
Performance Monitoring
Utilizing real-time data to monitor key performance indicators (KPIs) like order accuracy, picking speed, and inventory levels can provide insights into operational efficiency. By tracking these metrics, managers can identify bottlenecks and inefficiencies, enabling them to make informed decisions to optimize processes.
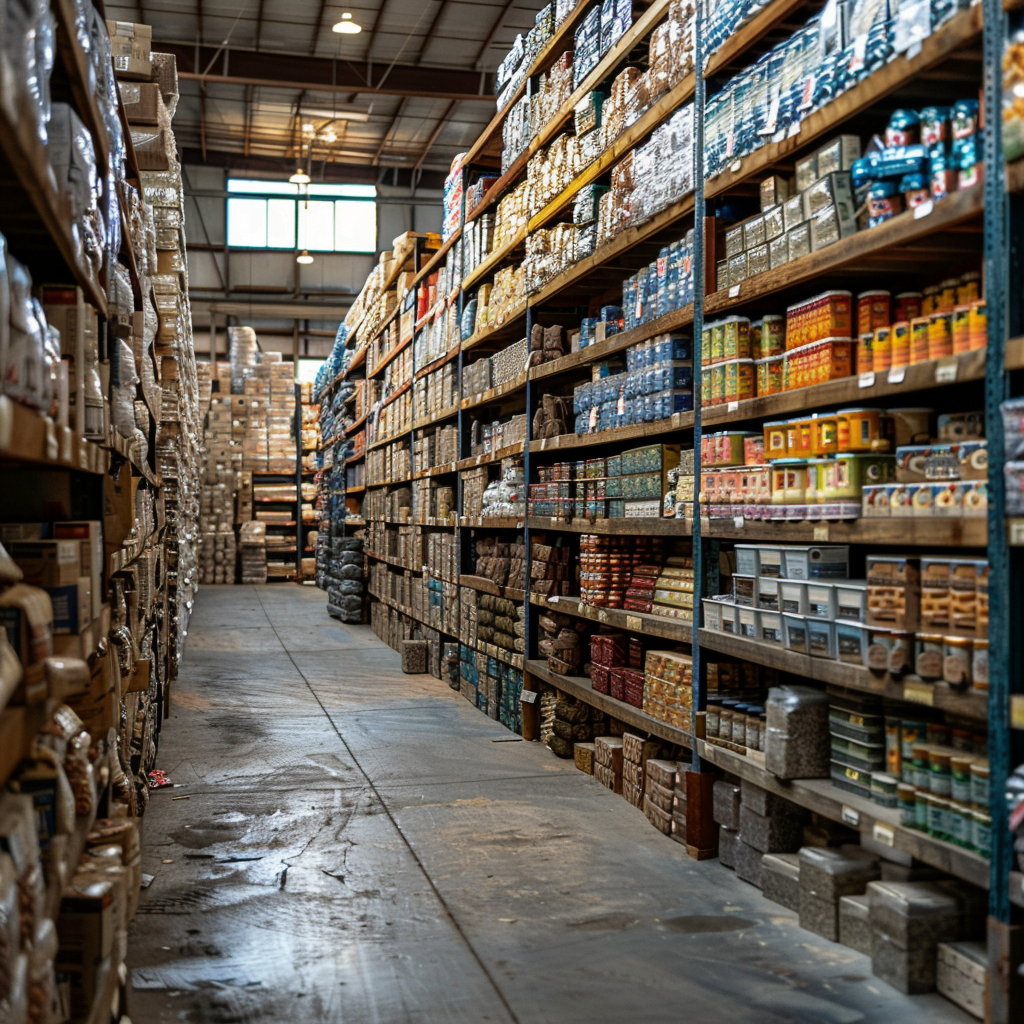
Predictive Analytics
Predictive analytics uses historical data to forecast future trends and demands. By applying predictive analytics, warehouses can anticipate inventory needs, adjust staffing levels, and plan for seasonal variations. This proactive approach helps in maintaining optimal inventory levels, reducing excess stock, and ensuring timely fulfillment of orders.
8. Cross-Docking
Implement Cross-Docking
Cross-docking involves directly transferring incoming goods to outbound shipping docks without storing them in the warehouse. This practice reduces handling and storage time, speeding up the material flow. Cross-docking is particularly useful for perishable goods or high-demand items, ensuring they reach customers quickly and efficiently.
9. Vendor Management
Collaborate with Suppliers
Working closely with suppliers can improve the efficiency of inbound shipments and reduce lead times. Establishing strong relationships and clear communication channels with suppliers ensures timely delivery of materials, minimizing delays and disruptions in the warehouse operations.
Just-In-Time Inventory
Adopting Just-In-Time (JIT) inventory practices involves receiving goods only when they are needed for production or sales. This approach reduces the need for excessive storage, lowers inventory carrying costs, and ensures a steady flow of materials, enhancing overall efficiency.
10. Technology Integration
IoT Devices
The Internet of Things (IoT) devices can provide real-time tracking of inventory and equipment. Sensors and smart devices can monitor the condition and location of goods, providing valuable data that can be used to optimize warehouse operations. IoT technology can also improve maintenance schedules for equipment, reducing downtime and enhancing productivity.
Cloud-Based Solutions
Cloud-based systems allow for better coordination and access to data from anywhere. By integrating cloud-based solutions, warehouses can improve communication, streamline operations, and enhance data sharing across different locations. This technology supports scalability and flexibility, enabling warehouses to adapt to changing demands quickly.
11. Ergonomic Enhancements
Ergonomic Equipment
Providing ergonomic tools and equipment can reduce physical strain on workers and improve efficiency. Adjustable workstations, lifting aids, and ergonomic hand tools can enhance worker comfort and productivity, reducing the risk of injuries and improving overall job satisfaction.
Adjustable Workstations
Adjustable workstations can accommodate different tasks and employee needs. By allowing workers to adjust the height and configuration of their workstations, you can create a more comfortable and efficient working environment. This flexibility can lead to increased productivity and reduced fatigue.
12. Quality Control
Regular Audits
Conducting regular quality control audits helps identify and address inefficiencies in processes and systems. These audits ensure that standards are maintained and that any issues are promptly corrected. Regular audits can lead to continuous improvements in quality and efficiency.
Standard Operating Procedures (SOPs)
Developing and enforcing Standard Operating Procedures (SOPs) ensures consistency and quality in operations. SOPs provide clear guidelines for employees to follow, reducing variability and errors. Regularly updating SOPs to reflect best practices and new technologies can further enhance operational efficiency.
Implementation Tips
Pilot Programs
Starting with pilot programs for new technologies or processes allows you to test their effectiveness before full-scale implementation. Pilots can provide valuable insights and help identify potential challenges, ensuring a smoother transition and higher chances of success.
Continuous Feedback
Maintaining an open line of communication with employees to gather feedback is crucial for continuous improvement. Encouraging employees to share their experiences and suggestions can help identify issues early and implement effective solutions, fostering a culture of collaboration and innovation.
Scalability
Ensuring that the strategies you implement are scalable is essential for accommodating future growth and changes in demand. Scalable solutions can be adjusted to meet the needs of a growing business, providing long-term benefits and maintaining efficiency as operations expand.