Most warehouses don’t get the luxury of starting with a blank slate. They grow over time—add a few...
Streamline warehouse movement with expert material flow evaluation.
Material Flow Evaluation
People – Equipment – Workflow
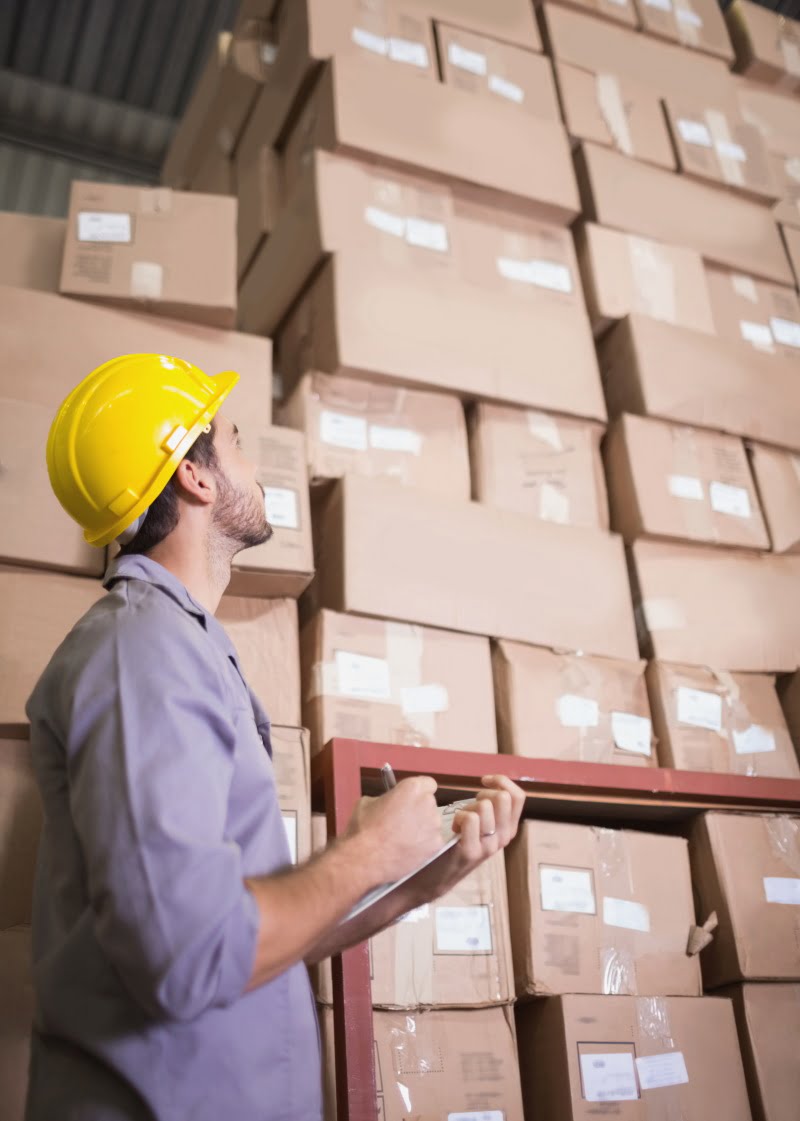
Material flow evaluation is a service designed to assess how materials move through your facility—reducing delays, improving efficiency, and eliminating bottlenecks. This service is ideal for warehouse managers, process engineers, and operations leaders looking to improve flow from receiving to shipping.
By examining physical layout, worker motion, and equipment use, we help you optimize your process and reduce unnecessary handling. Areas we typically assess include:
- Inbound receiving and putaway processes
- Product staging, picking, and packing flow
- Forklift and conveyor routing paths
- Workstation layout and material handling
- Shipping and outbound logistics zones
This evaluation improves throughput and builds a foundation for scalable, lean operations.
Warehouse Material Flow Optimization for Smoother Operations
Remove Bottlenecks
Improve Flow Efficiency
Build for Scalability
Learn More From Our Blog
How to Conduct a Material Flow Simulation
You can walk a warehouse a hundred times and still miss what a simulation shows in ten minutes....
How to Implement Material Flow Best Practices
In today's fast-paced business world, optimizing warehouse operations is crucial for companies to...
The Benefits of Agile Material Flow Systems
When it comes to warehouse operations, efficiency is key. Maximizing productivity and minimizing...
How to Use Mobile Technology to Enhance Material Flow
Warehouse operations can often be complex and challenging to manage. Efficient material flow is...
How to Address Material Flow Issues in Aging Warehouses
Have you noticed material flow issues in your aging warehouse? Are you struggling with...
Why Choose HCO Innovations for Material Flow Evaluation?
At HCO Innovations, we bring a practical, data-backed approach to material flow evaluation. Our team doesn’t just look at diagrams—we walk the floor, observe your operations, and develop real-world strategies that fit your unique facility layout. We focus on helping your people, products, and equipment move better, faster, and smarter.
- In-depth analysis of workflows from receiving to shipping
- Hands-on evaluation of equipment usage and motion paths
- Tailored layout and process improvement recommendations
- Focus on eliminating delays and increasing throughput
- Support for lean initiatives and operational scaling
If you’re looking to increase productivity without a full facility redesign, our material flow evaluations are a smart first step.
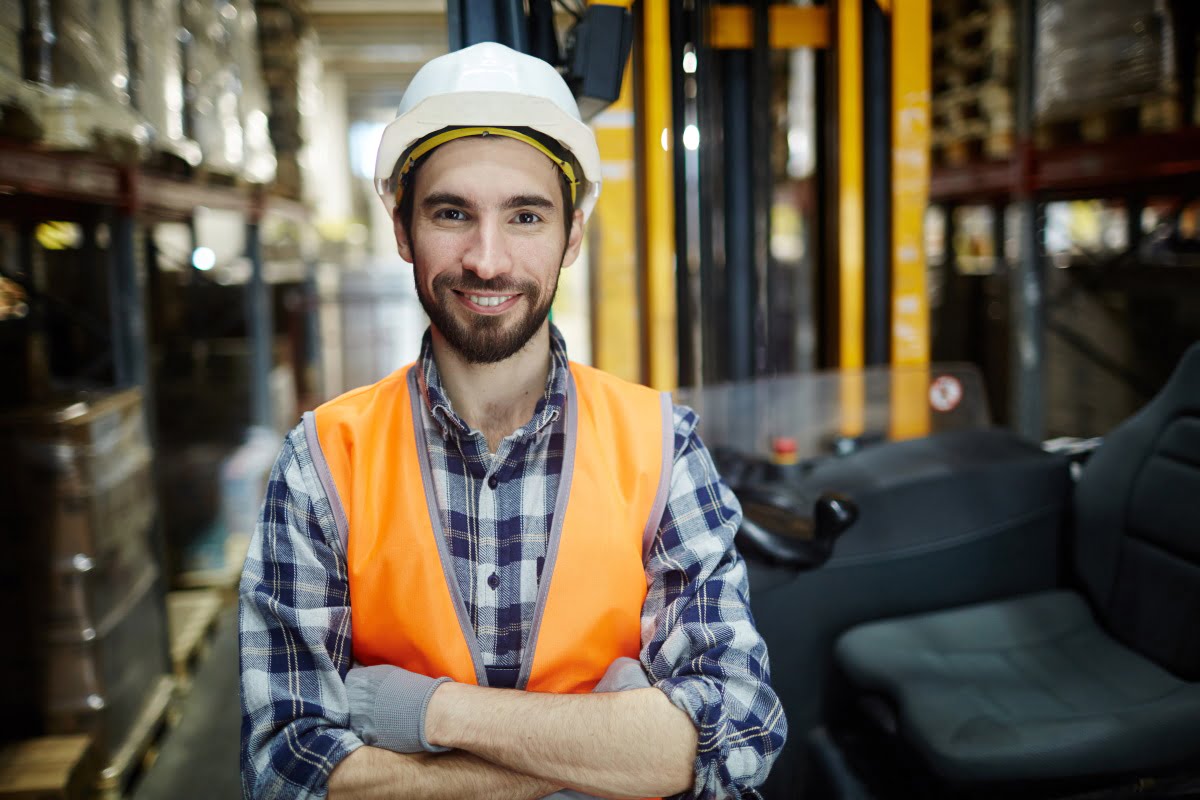