An efficient warehouse is an effective warehouse, so it is best for a warehouse to operate as smoothly as possible. When warehouse operations are fast and reliable, companies keep costs low, workers confident, and customers happy. Here are ten quick tips to help you improve your warehouse efficiency.
Tips For Improving Warehouse Efficiency
In the fast-moving world of warehouse management, efficiency is key to staying competitive and satisfying customer demands. Here are the top 10 quick tips for improving warehouse efficiency. Each tip offers straightforward, actionable advice that can help streamline operations, reduce costs, and boost overall productivity, ensuring your warehouse operates at its best.
1. Conduct A Warehouse AuditÂ
The first step into converting your warehouse into an efficient workplace is to conduct an operational audit. Identify critical metrics such as costs and productivity rates within your operational flow. This allows you to gauge the efficiency or inefficiency within the whole system.
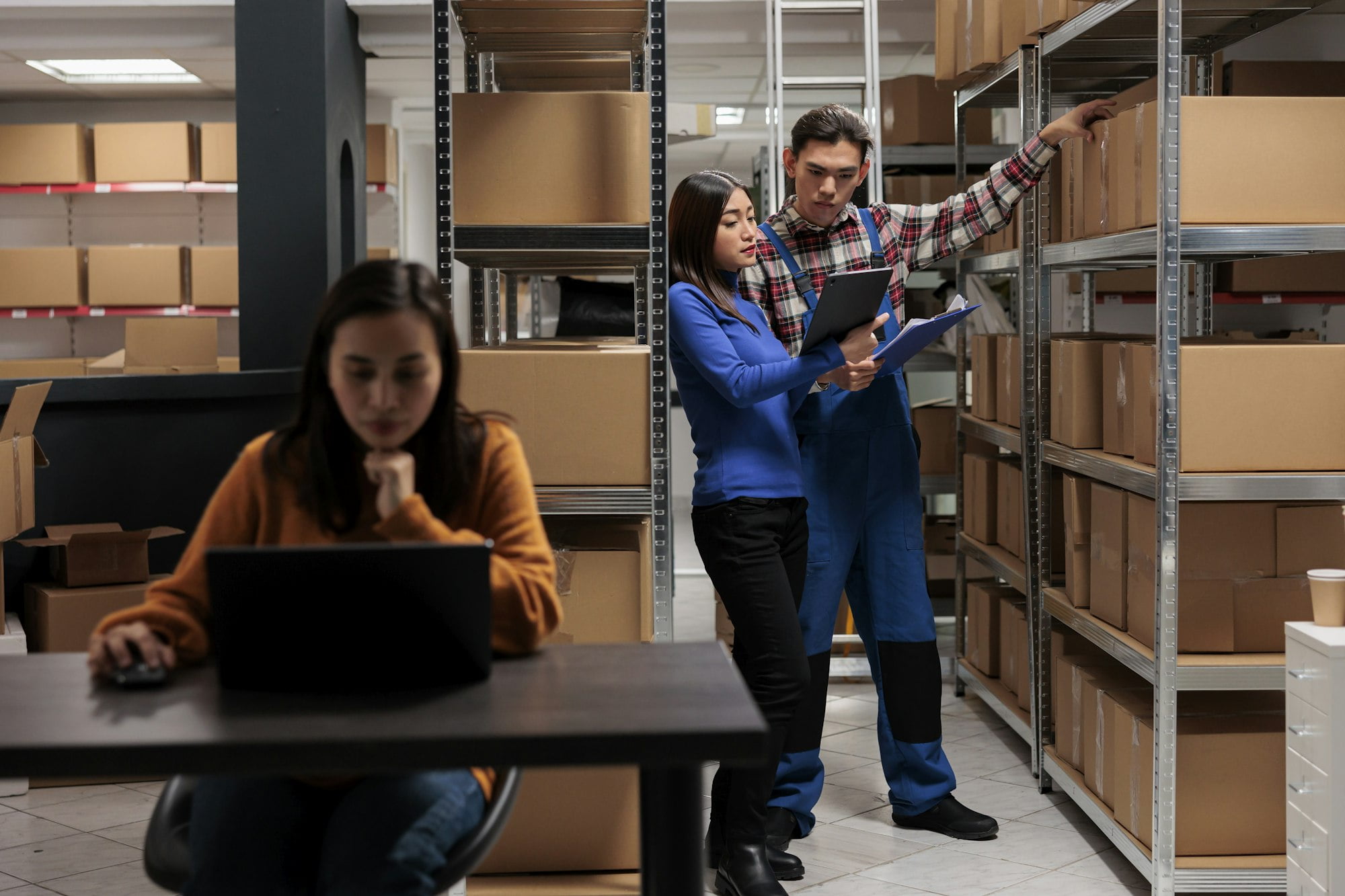
Warehouse worker and logistics manager doing products audit
An audit would help you recognize further or needed improvements, such as cost and error reduction, within the workflow.
2. Adopt A Lean Warehouse Operation
Maintain a lean methodology in operating your warehouse to reduce waste of any kind and only keep what you actually need. A lean warehouse cuts material handling time and decreases loading and unloading times of any vehicle. This also increases reliability, conciseness, and flexibility to adapt to market changes, simplifying processes, and reducing costs.
3. Maximize Warehouse Layout and Space
Establishing a good warehouse layout dramatically increases the efficiency of your warehouse. A well-thought-out warehouse plan reduces travel time between areas with more straightforward navigation and fewer safety hazards. Make sure your employees stick to the most efficient routes and follow correct procedures.
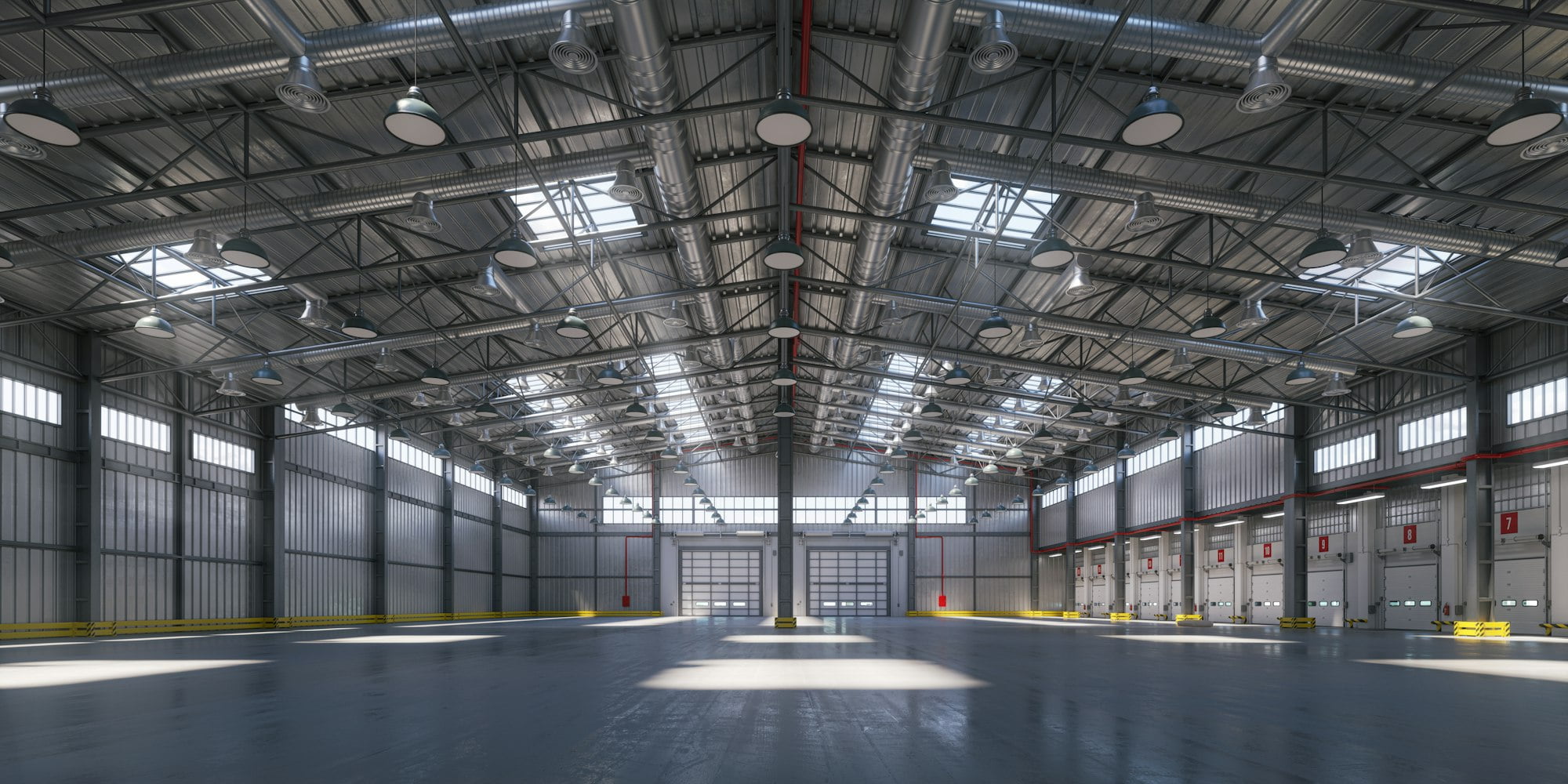
Empty warehouse or storehouse in daylight.
As for cubic space, make sure to use overhead areas adequately. This increases your facility’s utilization and maximizes the warehouse’s cost per square meter. However, always put safety first when erecting multilevel platforms.
4. Create An Inventory Hierarchy System
Using an inventory categorization system allows you to allocate proper resources to your most to the least valuable product or stock in terms of value. The hierarchy allows you to focus on prioritizing handling and security more closely of the items that make you the most money. This also ensures that you do not waste excessive time on less valuable items.
5. Invest In Your Warehouse Staff
Investing in your warehouse staff includes treating them fairly, providing regular training, and incentivizing good performance. Adopt an open-door policy allowing for openness in the workplace. Share productivity reports and other information freely, and ask for their opinions. All this leads to a corporate culture that creates confident, efficient, and knowledgeable employees.
6. Keep Your Warehouse Clean And Organized
An organized warehouse environment improves staff productivity and efficiency. Use the “5S” method of organizing workstations: Sort, Set in order, Shine, Standardize, and Sustain. This system speeds up daily processes, reduces errors, keeps the workplace clean, and improve overall safety. The method also allows employees to locate or retrieve equipment and items faster.
7. Optimize Picking Methodology
Determine whether the current picking methodology fits in your warehouse organization. As a core way to improve overall efficiency, using the right picking system directly influences the supply chain. Audit the current picking routes and processes to identify where you could save time. Also, consider upgrading picking equipment if it could improve your warehouse’s efficiency.
8. Analyze Supply Chain
Review whether the current supply chain flows smoothly, from the goods coming into goods going out. Develop compliance policies for everyone involved to reduce errors and the amount of time dealing with them. One broken link in a chain could lead to a broken system, costing you time and money.
9. Take Advantage Of Technology
Consider employing various warehouse technology to improve transaction accuracy and further reduce errors. A sound warehouse management system could include bar codes, radio frequency ID, voice-activated technology, and pick-to-label, automating processes.
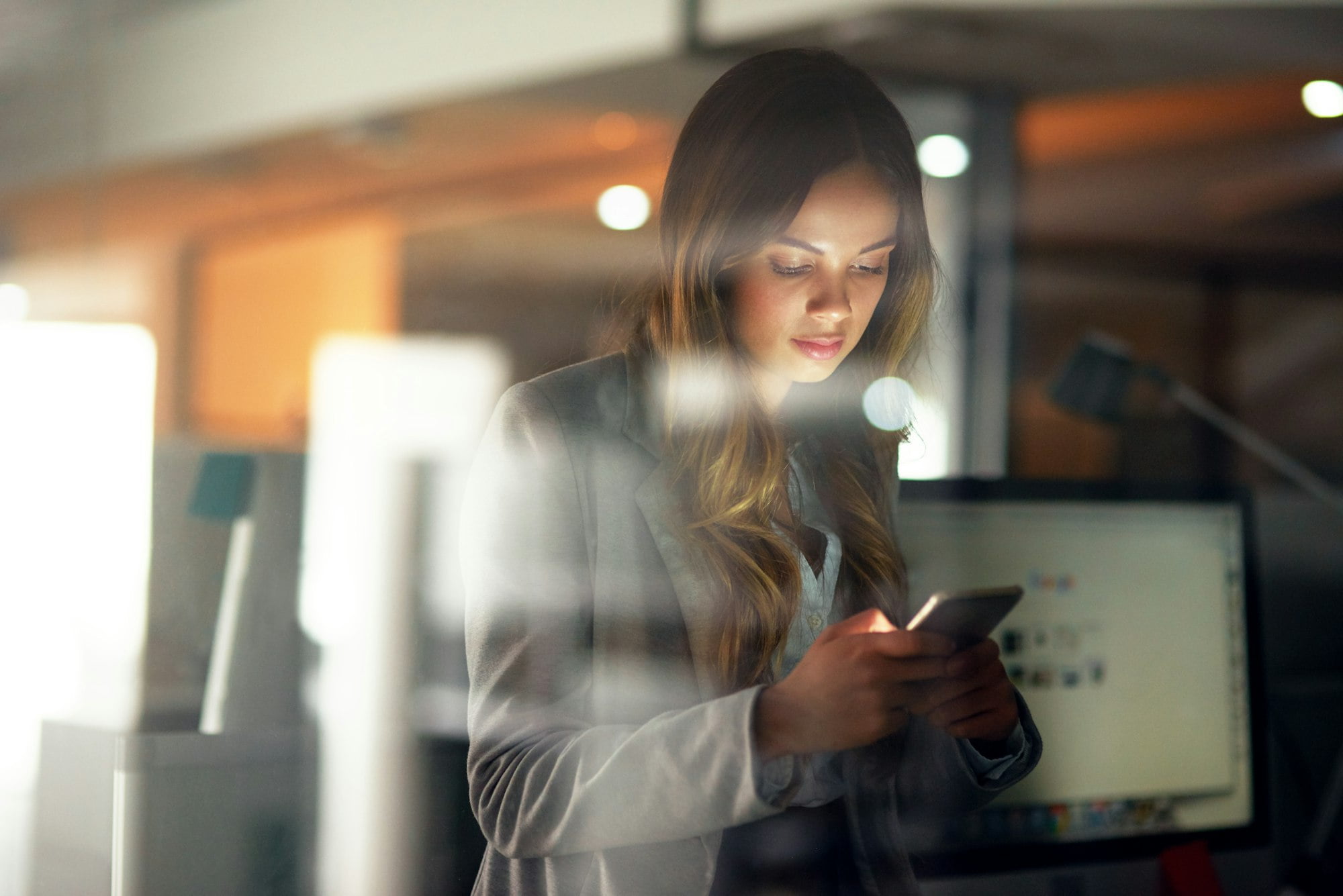
Taking advantage of these extra hours
These new technologies allow you to collect real-time data, track your inventory, and determine your warehouse’s efficiency. However, do your due diligence when buying from vendors.
10. Watch And Report Your Metrics
Monitoring your warehouse operating metrics and reporting them to your staff would positively improve efficiency. Most employees become more confident when they know how they measure up to established metrics. Setting up productivity measurements would improve overall labor efficiency and helps you keep track of activities. However, keep in mind not to set too many metrics so as not to overwhelm the system.
1. How can I improve warehouse efficiency?
Improving warehouse efficiency can be achieved by implementing various strategies such as optimizing layout, implementing proper inventory management systems, utilizing technology like barcode scanning and automation, and investing in employee training programs.
2. What role does organization play in warehouse efficiency?
Organization is crucial for warehouse efficiency. By maintaining a well-organized warehouse with designated storage spaces, properly labeled products, and easy accessibility, you can minimize errors, reduce picking time, and enhance overall productivity.
3. How can I reduce inventory errors?
To reduce inventory errors, it's important to implement an efficient inventory management system. Utilize barcode scanning or RFID technology to accurately track products, conduct regular audits, perform cycle counts, and ensure all team members are properly trained on inventory management procedures.
4. What are some techniques to improve order picking speed?
To improve order picking speed, consider using methods such as batch picking, zone picking, or wave picking. Additionally, optimize your warehouse layout to minimize travel time, ensure clear product labeling, and provide training to staff on efficient picking techniques.
5. How can I optimize space utilization in my warehouse?
To optimize space utilization, analyze your warehouse layout and consider implementing techniques such as vertical storage systems, mezzanine floors, or compact shelving. Additionally, review your inventory turnover rates and relocate slow-moving items to less accessible areas.
6. What is the role of technology in improving warehouse efficiency?
Technology plays a vital role in improving warehouse efficiency. Warehouse management systems (WMS), barcode scanning, automated conveyor systems, and robotics can streamline processes, reduce manual errors, and improve overall productivity.
7. How can I improve employee productivity in the warehouse?
To improve employee productivity, offer regular training for new employees and ongoing training to enhance skills. Establish clear performance metrics, provide incentives, and encourage teamwork. Also, consider regular performance reviews and provide feedback to motivate and empower your workforce.
8. How can I minimize product damage during handling?
To minimize product damage, ensure proper training for employees in safe handling techniques. Use suitable packaging materials, implement quality control checks during receiving and shipping, and regularly inspect warehouse equipment to avoid any potential hazards.
9. What role does data analysis play in warehouse efficiency?
Data analysis is crucial for identifying areas of improvement in warehouse efficiency. By analyzing order data, inventory levels, and employee performance, you can make data-informed decisions, identify bottlenecks, and implement strategies to enhance overall efficiency.
10. How often should I review and update my warehouse processes?
Regularly reviewing and updating warehouse processes is essential for continuous improvement. Aim for quarterly or bi-annual reviews to identify inefficiencies, recognize emerging trends, adapt to changing customer demands, and proactively address any issues that may arise.
Top 10 Warehouse Safety Practices You Should Implement.
Warehouse safety is of utmost importance in any industry that involves material handling and storage. Implementing effective safety practices not only ensures the well-being of the workers but also leads to increased productivity and cost savings for the company. At HCO Innovations, we specialize in warehouse optimization and forklift fleet management, and we understand the significance of a safe and secure working environment. In this article, we will discuss the top 10 warehouse safety practices that you should implement to create a safe workplace for your employees.
1. Employee Training and Education
Proper training and education of warehouse personnel is the foundation of a safe workplace. Employees should receive comprehensive training on operating equipment, handling hazardous materials, and following safety protocols. Conduct regular refresher courses to reinforce knowledge and promote a safety-conscious culture.
2. Clear Communication and Signage
Clear communication is essential to ensure that everyone in the warehouse understands safety procedures and protocols. Use appropriate signage to indicate potential hazards, emergency exits, and safety equipment locations. Regularly check and replace damaged or faded signs.
3. Regular Equipment Maintenance
Maintaining equipment, including forklifts, pallet jacks, and conveyor systems, is crucial for safe operations. Regular inspections, maintenance, and repairs will minimize the risk of accidents caused by equipment malfunctions.
4. Proper Material Storage
Organize your warehouse by implementing proper storage practices. Keep heavy items on lower shelves to prevent toppling, and ensure that all items are stored securely. Use racks, shelves, and storage containers designed for specific types of materials.
5. Implement a Comprehensive Housekeeping Program
A clean and well-organized warehouse reduces the risk of accidents. Implement a regular housekeeping program to keep the floors free of obstacles, spills, and debris. Encourage employees to report any safety hazards they come across during their work shifts.
6. Personal Protective Equipment (PPE)
Provide appropriate personal protective equipment to all warehouse workers. This may include items such as hard hats, safety glasses, steel-toed boots, gloves, and high-visibility vests. Train employees on the correct usage and maintenance of PPE.
7. Emergency Preparedness
Develop and practice emergency response procedures to handle situations such as fires, chemical spills, and medical emergencies. Ensure that all employees are aware of evacuation routes and assembly points.
8. Regular Safety Inspections
Conduct regular safety inspections to identify any potential hazards or safety violations. Engage employees in the inspection process and encourage them to report any safety concerns they observe.
9. Ergonomics and Injury Prevention
Implement ergonomic principles to reduce the risk of musculoskeletal injuries. Provide proper lifting and handling techniques training to employees. Use equipment and tools with ergonomic features to minimize physical strain.
10. Continuous Improvement
Regularly review and analyze safety performance and incidents to identify areas for improvement. Implement corrective actions and make necessary changes to ensure a safe working environment. Encourage feedback from employees to foster a culture of continuous improvement.
By implementing these top 10 warehouse safety practices, you can create a workplace that prioritizes the well-being of your employees. At HCO Innovations, we understand the critical importance of safety in warehouse operations. Our comprehensive services, including warehouse layout evaluation and safety assessments, can help you optimize your warehouse and implement effective safety practices. Contact us today at HCO Innovations to learn more about our solutions for warehouse optimization and forklift fleet management.