Optimizing warehouse operations is crucial for businesses looking to enhance efficiency and reduce operational costs. By leveraging strategic planning and modern technology, warehouses can significantly improve their functionality and productivity, adapting to the demands of a dynamic market. In this article, you will learn about Unlocking Your Warehouse’s Potential.
Unlocking Your Warehouse’s Potential by Conducting a Layout Evaluation
This guide offers a comprehensive approach to refining operational efficiency and embracing innovation within your logistical hubs. Focused on optimizing spatial utilization and process streamlining, it provides actionable insights into adopting cutting-edge technologies and best practices in inventory management. Enhance productivity and transform your facility’s functionality with expert strategies designed to tap into its full potential.
Significance of Efficient Warehouse Management
Efficient warehouse management is essential for maintaining cost-effectiveness and timely customer service in today’s competitive market. It involves the systematic organization of inventory, enhancement of workflows, and utilization of every square foot of storage space to minimize costs while maximizing output.
Challenges in Modern Warehouse Operations
Warehouse operations face numerous challenges, including fluctuating demands, labor shortages, and the need for technological upgrades. These obstacles require innovative solutions to streamline operations, enhance storage capacities, and maintain a competitive edge.
Comprehensive Assessment of Current Operations
To optimize a warehouse, it is vital to begin with a thorough assessment of the existing operations, pinpointing areas that require improvement and identifying opportunities for growth.
Conducting a Thorough Capacity Analysis
A detailed capacity analysis involves examining the current usage of warehouse space, understanding inventory turnover rates, and evaluating the effectiveness of existing storage solutions. This analysis helps to identify inefficiencies and plan for more strategic use of space.
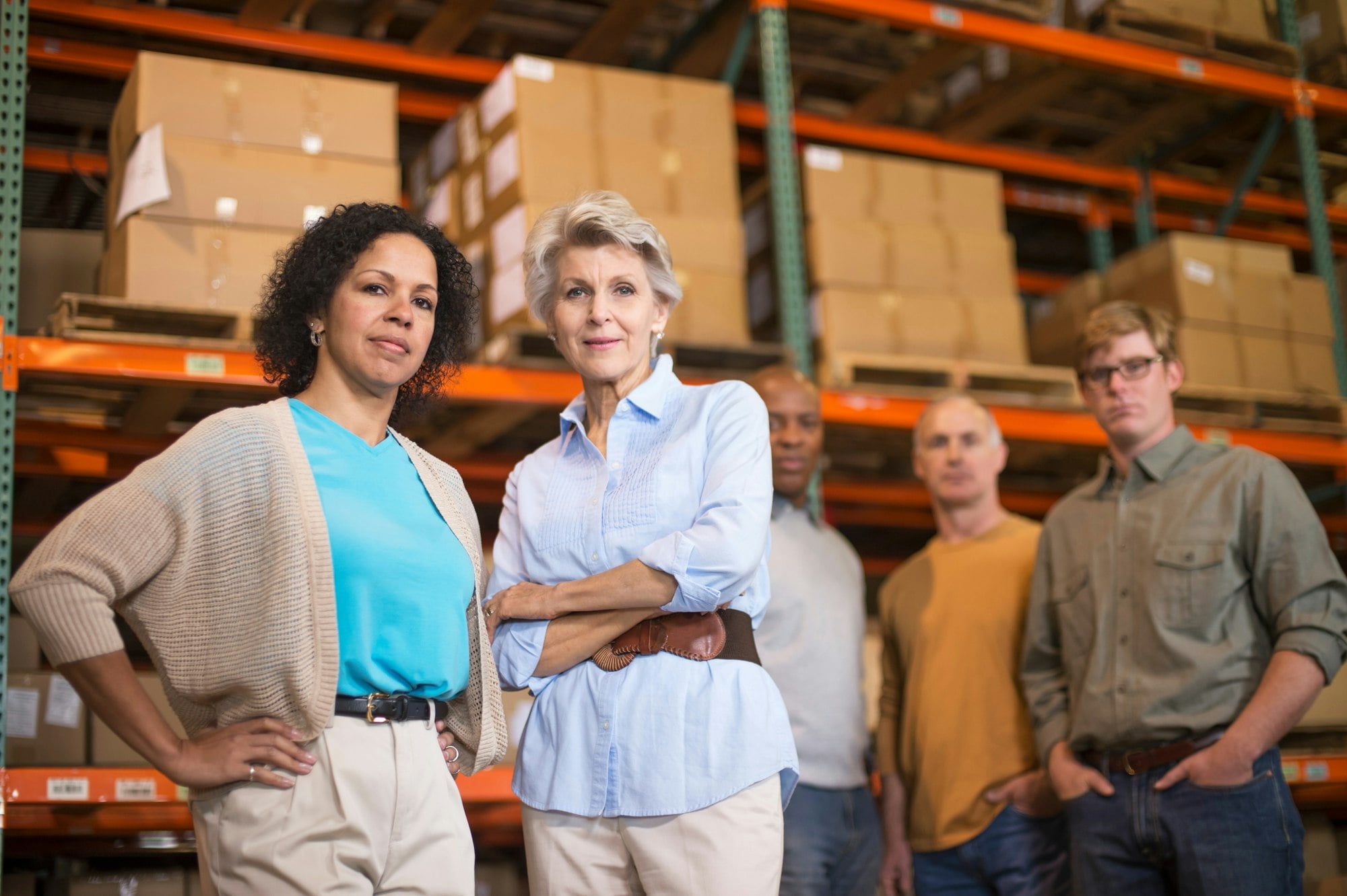
Portrait of warehouse workers in front of boxes
Key Performance Indicators for Warehouse Efficiency
Monitoring key performance indicators (KPIs) such as order accuracy, inventory levels, and fulfillment times is fundamental. These metrics provide insights into operational performance and help managers make informed decisions to boost productivity.
Warehouse Layout and Design Strategies
An effective warehouse layout is pivotal for optimizing operations. It should facilitate a logical flow of materials, minimize handling, and support scalability as business needs change.
Optimizing Space Utilization and Flow
Utilizing every inch of available space through smart design solutions such as vertical storage, multi-tiered systems, and automated storage and retrieval systems (AS/RS) can transform a cramped warehouse into a streamlined operation.
Strategic Placement of Goods for Accessibility
Strategically organizing inventory to place frequently accessed items near processing areas minimizes travel time and speeds up the order fulfillment process, significantly boosting efficiency.
Incorporating Flexibility and Scalability into Design
Designing a warehouse to be flexible and scalable allows for adjustments in layout and storage capacity to accommodate growth or changes in inventory types without significant disruptions.
Technological Innovations in Warehouse Management
The adoption of advanced technologies in warehouse management not only streamlines operations but also provides significant cost reductions and accuracy improvements.
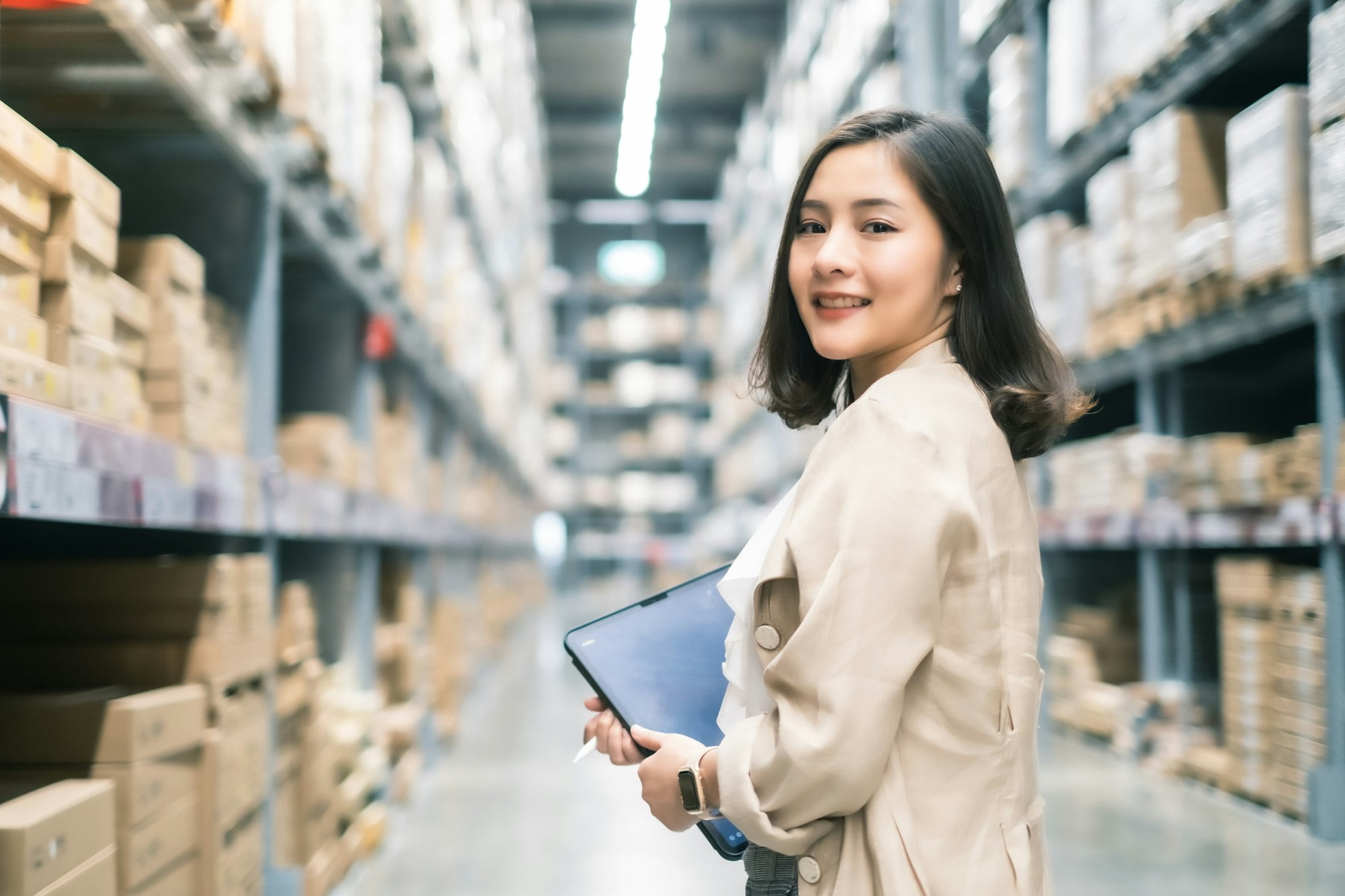
BUSINESS WAREHOUSE
Automation: Robots and Conveyor Belts
Implementing automation in the form of robotics and conveyor systems can greatly enhance speed and accuracy in material handling, reducing reliance on manual labor and minimizing errors.
The Role of Warehouse Management Systems
Warehouse Management Systems (WMS) play a critical role in optimizing operations by providing real-time data on inventory and facilitating efficient resource and space management.
Implementing RFID and Barcode Systems
Radio Frequency Identification (RFID) and barcode systems improve inventory tracking and management, offering precise control over stock levels and significantly reducing the likelihood of errors.
Inventory Management Best Practices
Effective inventory management is key to optimizing warehouse efficiency. It ensures that inventory is well-organized, easily accessible, and adequately stocked to meet demand without excessive surplus.
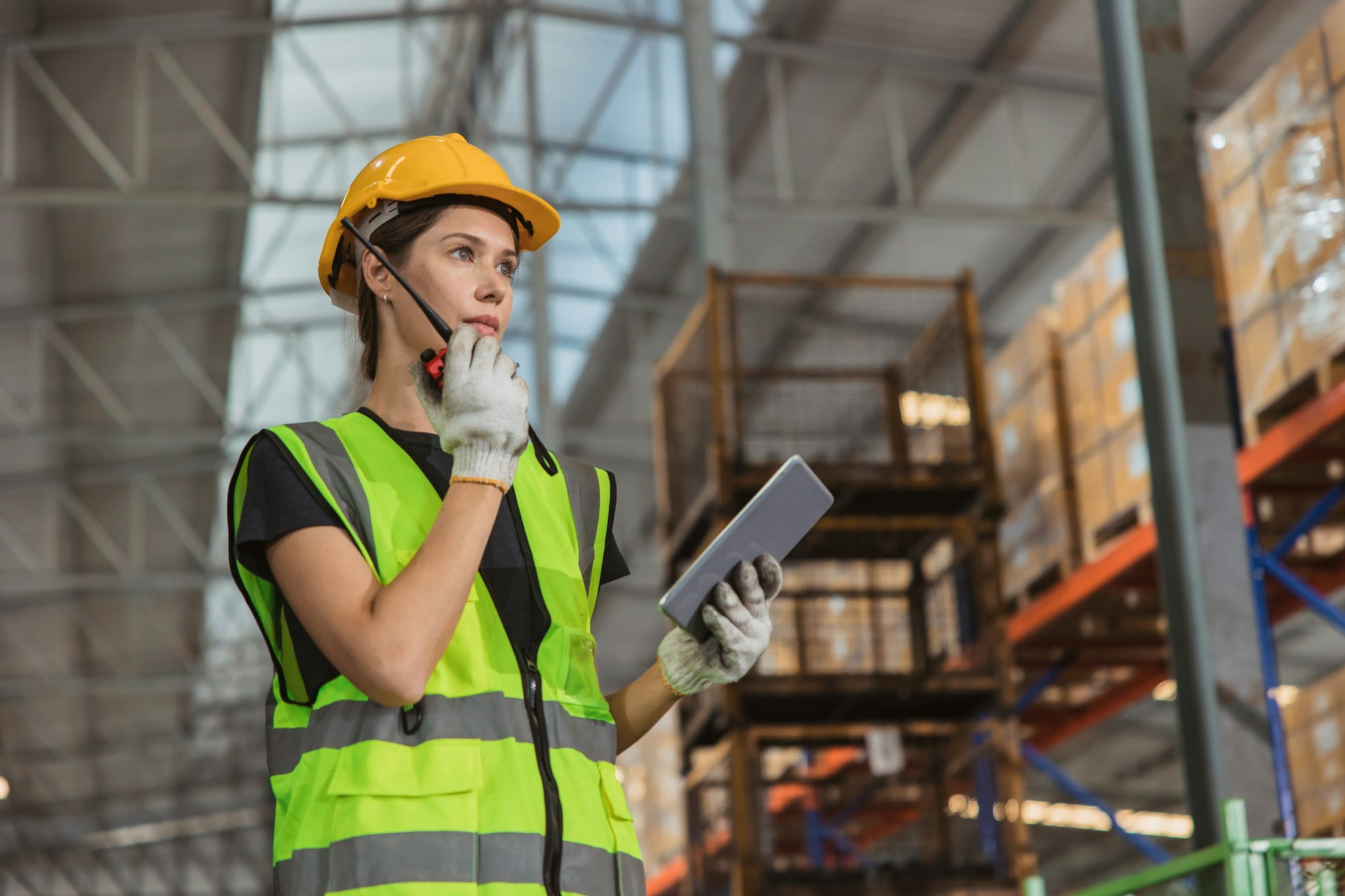
working woman staff worker engineer foreman inventory management supervisor team radio control
Adopting ABC Analysis for Inventory Prioritization
ABC analysis categorizes inventory based on importance and turnover rates, helping warehouses prioritize space and resources for high-demand items, thus optimizing the overall storage strategy.
Enhancing Forecasting Techniques for Better Planning
Advanced forecasting techniques allow warehouses to anticipate demand changes, adjust inventory levels accordingly, and avoid both overstock and stockout situations.
Reducing Stock Levels and Avoiding Overstocking
Maintaining optimal stock levels through precise demand forecasting and inventory reviews prevents overstocking, which ties up capital and reduces storage space efficiency.
Applying Lean Management Principles
Lean management principles focus on reducing waste and improving efficiency through continuous improvement and respect for people.
Utilizing 5S for Organizational Efficiency
The 5S methodology (Sort, Set in Order, Shine, Standardize, Sustain) is an effective tool for organizing workspace to enhance efficiency and safety in warehouse operations.
Continuous Improvement and Waste Reduction
Adopting a culture of continuous improvement involves regularly seeking ways to refine processes and eliminate waste, which contributes to leaner and more efficient operations.
Enhancing Workforce Efficiency
A well-trained and motivated workforce is essential for maintaining efficient operations and achieving high productivity levels in any warehouse setting
Developing Effective Training Programs
Developing comprehensive training programs ensures that all employees understand their roles and the technology at their disposal, thereby enhancing operational efficiency and reducing errors.
Cultivating a Safe and Productive Work Environment
A focus on safety and productivity not only reduces the risk of accidents but also promotes a more engaged and efficient workforce, directly impacting the bottom line.
Role of Employee Satisfaction in Operational Efficiency
Ensuring employee satisfaction is crucial for maintaining low turnover rates and high productivity. Satisfied employees are more likely to contribute positively to operations and embrace company initiatives.
Integrating Advanced Planning and Operations
Strategic planning and advanced operational techniques are vital for optimizing warehouse functionality and responding effectively to market dynamics.
Strategic Resource Allocation and Scheduling
Efficient allocation of resources and precise scheduling ensure optimal operation, enabling warehouses to meet demand spikes without undue stress on the system.
Adapting to Market Changes and Demand Fluctuations
Warehouses must be agile, adapting quickly to market changes and demand fluctuations to maintain service levels and avoid inventory imbalances.
Conclusion
Key Takeaways and Strategic Insights
This article provides a roadmap for warehouse optimization, emphasizing strategic planning, technology integration, and workforce management to unlock the full potential of warehouse operations.
Future Trends in Warehouse Optimization
Looking forward, the use of AI and machine learning in inventory and operations management is expected to redefine warehouse efficiencies, offering even greater precision and adaptability to changing market conditions.
What is a layout evaluation for a warehouse?
A layout evaluation for a warehouse is a systematic assessment of the physical arrangement and organization of the warehouse space. It involves analyzing the current layout to identify areas of improvement and implementing changes to optimize efficiency, productivity, and safety.
Why is a layout evaluation important for warehouses?
A layout evaluation is important for warehouses because it helps identify bottlenecks, inefficiencies, and safety hazards within the facility. By understanding the current layout and making appropriate improvements, warehouses can enhance workflow, reduce operational costs, increase storage capacity, and improve overall productivity.
When should a warehouse conduct a layout evaluation?
A warehouse should conduct a layout evaluation when there are significant changes in operations, such as increased product volume, changes in product mix, or shifts in customer demands. Additionally, conducting a layout evaluation periodically, even without major changes, can help ensure that the warehouse is operating at maximum efficiency.
What are the key steps in conducting a comprehensive layout evaluation?
The key steps in conducting a comprehensive layout evaluation include:
- Collecting data on current operations and inventory levels
- Mapping out the existing layout and identifying problem areas
- Analyzing workflow patterns and material handling processes
- Brainstorming potential layout improvements
- Creating and implementing a new layout plan
- Monitoring and evaluating the effectiveness of the new layout
Can a layout evaluation impact warehouse safety?
Yes, a layout evaluation can significantly impact warehouse safety. By identifying and addressing safety hazards such as obstructed emergency exits, poor lighting, or congested areas, a layout evaluation can help create a safer working environment for employees. It can also facilitate better organization and placement of safety equipment, signage, and training materials.
Does a layout evaluation require specialized expertise?
While a layout evaluation can be conducted by employees familiar with warehouse operations, specialized expertise can provide valuable insights and guidance. Engaging professionals with experience in warehouse layout design, operations planning, and logistics can help ensure a thorough and effective evaluation, leading to optimal layout improvements.
How long does a layout evaluation process typically take?
The duration of a layout evaluation process varies depending on the size and complexity of the warehouse, as well as the scope of changes required. While smaller warehouses may be evaluated within a few weeks, larger and more intricate facilities could take several months from initial assessment to final implementation.
What are some common challenges faced when conducting a layout evaluation?
Common challenges when conducting a layout evaluation include resistance to change, disruption to ongoing operations, capital and resource constraints, and balancing the trade-offs between conflicting objectives such as storage capacity and accessibility. It is essential to carefully plan and communicate the evaluation process to overcome these challenges and ensure successful implementation.
Having an efficient warehouse storage system can greatly impact the success and profitability of your business. A well-organized and optimized warehouse can maximize space utilization, streamline operations, and ultimately reduce costs. In this article, we will explore some key strategies and best practices for creating an efficient warehouse storage system.
1. Analyze and Optimize Warehouse Layout
A crucial first step in creating an efficient warehouse storage system is to analyze and optimize your warehouse layout. This involves evaluating the existing space, identifying bottlenecks or inefficiencies, and implementing changes to improve workflow.
Consider the flow of materials and the movement of forklifts and other equipment within the warehouse. Are there any areas where congestion occurs or where materials frequently get lost or misplaced? By identifying these pain points, you can make informed decisions about repositioning racks, adjusting aisle widths, or implementing a better inventory management system.
An experienced warehouse optimization consulting firm like HCO Innovations can provide valuable insights and recommendations based on their expertise in warehouse layout evaluation.
2. Utilize Vertical Space with Racking Systems
Maximizing vertical space is a key aspect of efficient warehouse storage. By utilizing racking systems, you can effectively use the available vertical space, allowing for more storage and better organization. Racking systems come in various types, including selective racks, push-back racks, and drive-in racks, each with its own advantages and best-fit applications.
Selective racks, for example, are ideal for warehouses with a wide variety of products and SKUs, as they allow easy access to each individual pallet. On the other hand, push-back racks are better suited for high-density storage of multiple pallets of the same product.
Working with a warehouse optimization specialist can help you determine the most suitable racking systems for your specific requirements based on product characteristics, inventory turnover, and space constraints.
3. Implement a Warehouse Management System
A warehouse management system (WMS) is a software solution that helps streamline warehouse operations and optimize inventory management. A WMS can automate tasks such as receiving, picking, packing, and shipping, reducing human errors and improving overall efficiency.
By implementing a WMS, you can also gain real-time visibility into inventory levels, track product movement, and generate accurate reports for better decision-making. This level of automation and data accuracy can significantly improve order fulfillment and customer satisfaction.
Together with a forklift fleet management software, a WMS can further enhance operational efficiency by optimizing forklift routes, scheduling maintenance, and providing real-time monitoring of forklift performance.
4. Prioritize Safety and Training
Safety should be a top priority in any warehouse environment. Implementing safety measures not only protects your employees but also helps prevent damaged products and costly accidents.
Regularly inspect and maintain equipment like forklifts to ensure they are in proper working condition. Train employees on proper handling and operating procedures, and provide them with personal protective equipment.
In addition to safety training, ongoing employee training programs can also improve efficiency and productivity. Cross-training employees to handle different tasks can help reduce downtime during peak periods or when employees are absent.
5. Regularly Review and Optimize Processes
Creating an efficient warehouse storage system is an ongoing process. Regularly review your warehouse processes and identify areas for improvement. Keep track of key performance indicators (KPIs) such as order fulfillment time, inventory accuracy, and returns, and identify any trends or issues that need to be addressed.
Use your findings to implement changes, refine processes, and continue optimizing your warehouse storage system. Consult with industry experts like HCO Innovations to stay updated on the latest trends and technologies in warehouse optimization.
By following these strategies and best practices, you can create an efficient warehouse storage system that maximizes space utilization, streamlines operations, and ultimately improves your bottom line. Remember, optimizing your warehouse is an ongoing process, so keep evaluating, refining, and adapting to stay ahead of the competition.
For more information on warehouse optimization and forklift fleet management solutions, visit HCO Innovations.