Understanding the differences between a warehouse and a distribution center is crucial for businesses that aim to optimize their supply chain and logistics operations. Although both facilities handle goods, their roles, functions, and operational structures vary significantly. This article explores these differences comprehensively, covering definitions, functions, inventory management, location, technology, costs, benefits, drawbacks, and real-world examples. Learn more about warehouse network optimization for more insights on optimizing your logistics network. This knowledge is essential when comparing Warehouse vs Distribution Center to determine the best fit for your business needs.
Warehouse vs Distribution Center (Differences)
The terms warehouse and distribution center are often used interchangeably, but they serve distinct purposes within the supply chain.
Warehouse
A warehouse is a storage facility where goods are kept for long periods. Its primary role is to store products until they are needed. Warehouses are generally simpler in terms of operations compared to distribution centers. They provide a controlled environment for inventory, ensuring products are preserved and protected over time.
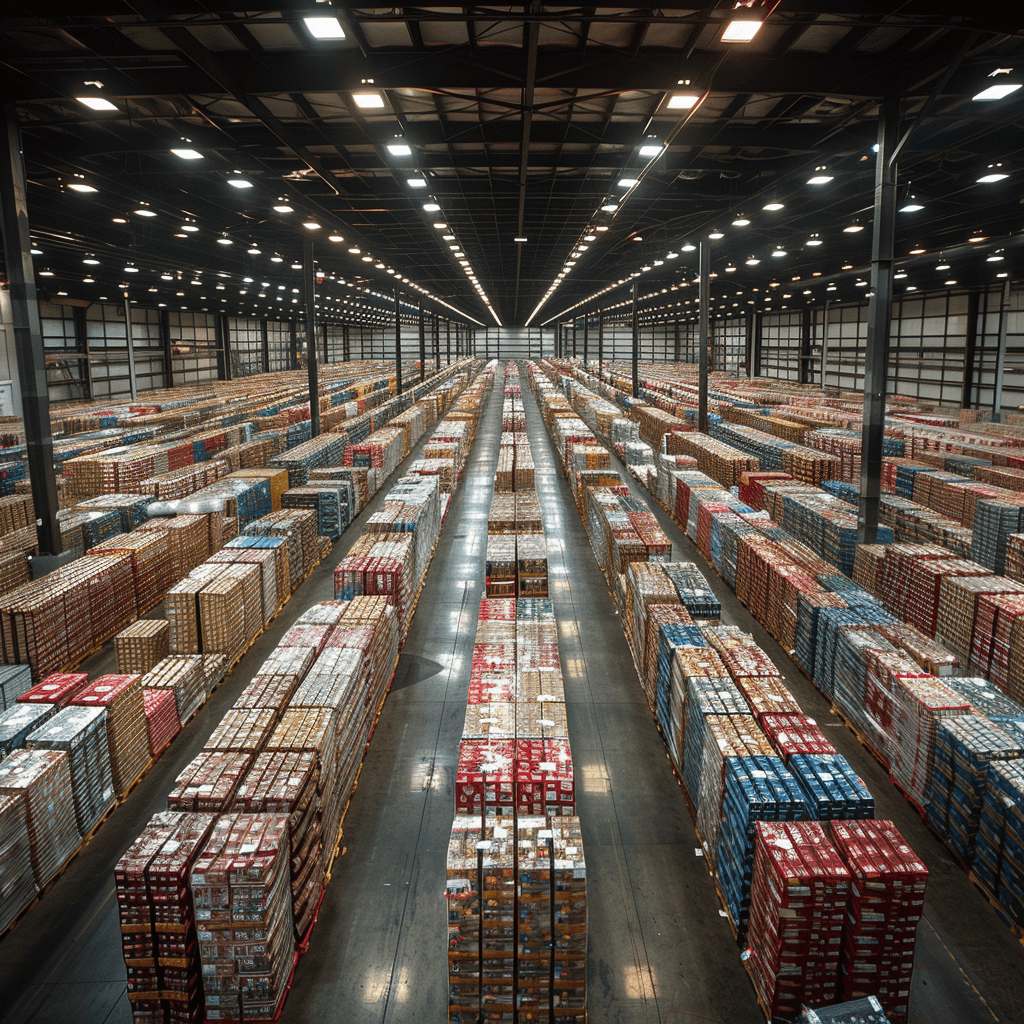
Distribution Center
A distribution center is a facility that focuses on the efficient and rapid turnover of goods. It serves as a hub for receiving, sorting, and shipping products to various destinations. Unlike warehouses, distribution centers emphasize quick movement rather than long-term storage. They are integral to order fulfillment processes, ensuring that products reach customers promptly.
Functions and Operations
The core functions and operations of warehouses and distribution centers highlight their distinct roles in the logistics chain.
Warehouse Functions
Warehouses are designed to store, preserve, and protect goods. They provide an organized environment where inventory control, stock rotation, and loading/unloading are essential operations. These facilities ensure that products are kept safe and maintained in good condition until they are required.
- Inventory Control: Warehouses maintain detailed records of all stored items, ensuring accurate tracking and management of stock levels.
- Stock Rotation: Implementing practices like FIFO (First-In-First-Out) to ensure older stock is used first, reducing the risk of spoilage or obsolescence.
- Loading/Unloading: Efficiently handling the receipt and dispatch of goods to and from the warehouse.
Distribution Center Functions
Distribution centers handle order fulfillment, cross-docking, packaging, and shipping. Their operations are geared towards rapid processing, high inventory turnover, and efficient dispatching to meet customer demands quickly.
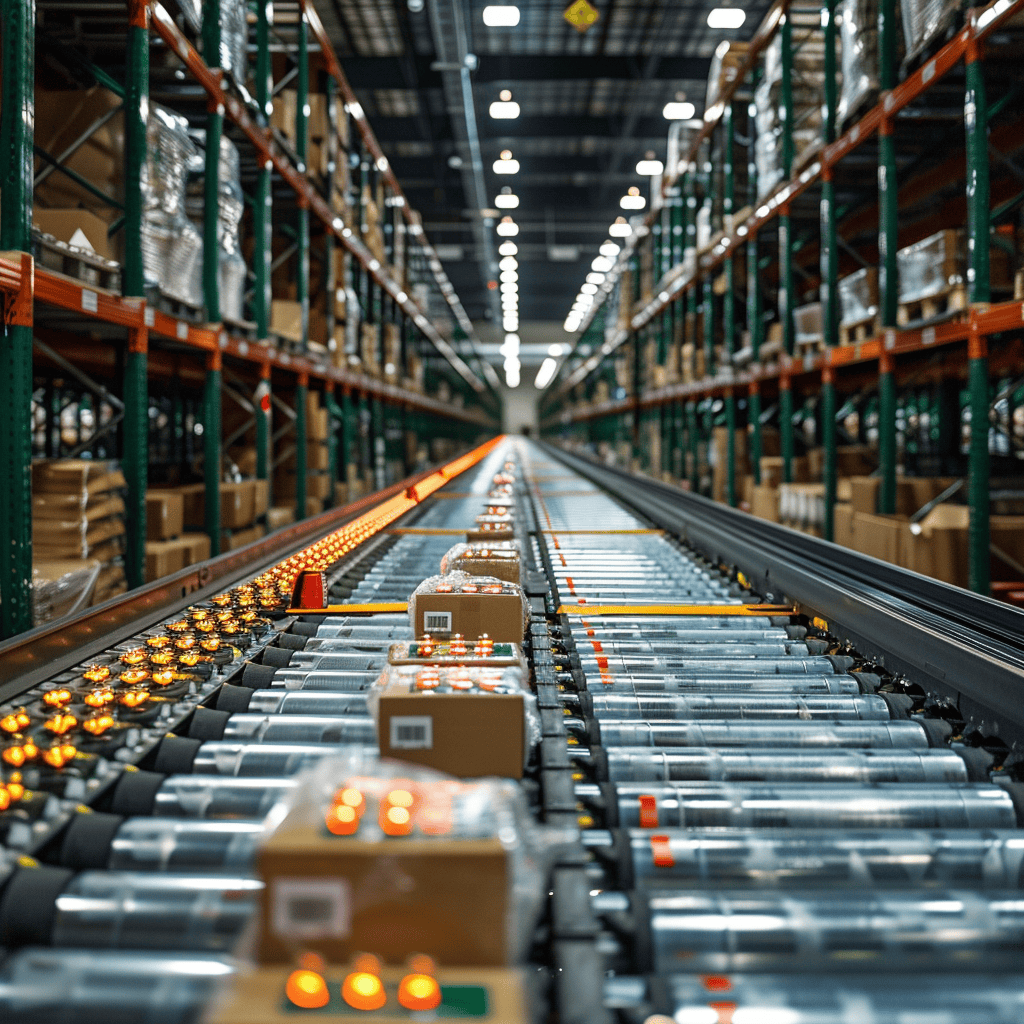
- Order Fulfillment: Processing customer orders promptly to ensure timely delivery.
- Cross-Docking: Receiving products and immediately preparing them for shipment without long-term storage, reducing handling and storage costs.
- Packaging and Shipping: Ensuring products are correctly packaged and shipped efficiently to their destinations.
Inventory Management
Effective inventory management is critical for both warehouses and distribution centers, though their approaches differ.
Warehouse Inventory Management
Warehouses manage bulk storage with a focus on maintaining accurate stock levels and ensuring inventory accuracy. They are well-suited for storing large quantities of goods for extended periods.
- Bulk Storage: Holding significant amounts of inventory, often organized by product type or SKU.
- Stock Levels: Monitoring and maintaining optimal stock levels to meet future demand without overstocking.
- Inventory Accuracy: Regular audits and checks to ensure records match physical inventory.
Distribution Center Inventory Management
Distribution centers utilize just-in-time inventory strategies, dynamic allocation, and maintain high order accuracy. Their inventory management systems are designed for efficiency and rapid turnover.
- Just-In-Time Inventory: Keeping minimal inventory on hand, receiving goods as they are needed to fulfill orders.
- Dynamic Allocation: Adjusting stock levels and allocation based on real-time demand and supply chain variables.
- Order Accuracy: Ensuring that orders are picked, packed, and shipped correctly to meet customer expectations.
Location and Accessibility
The location and accessibility of warehouses and distribution centers are strategic decisions that impact their efficiency and effectiveness.
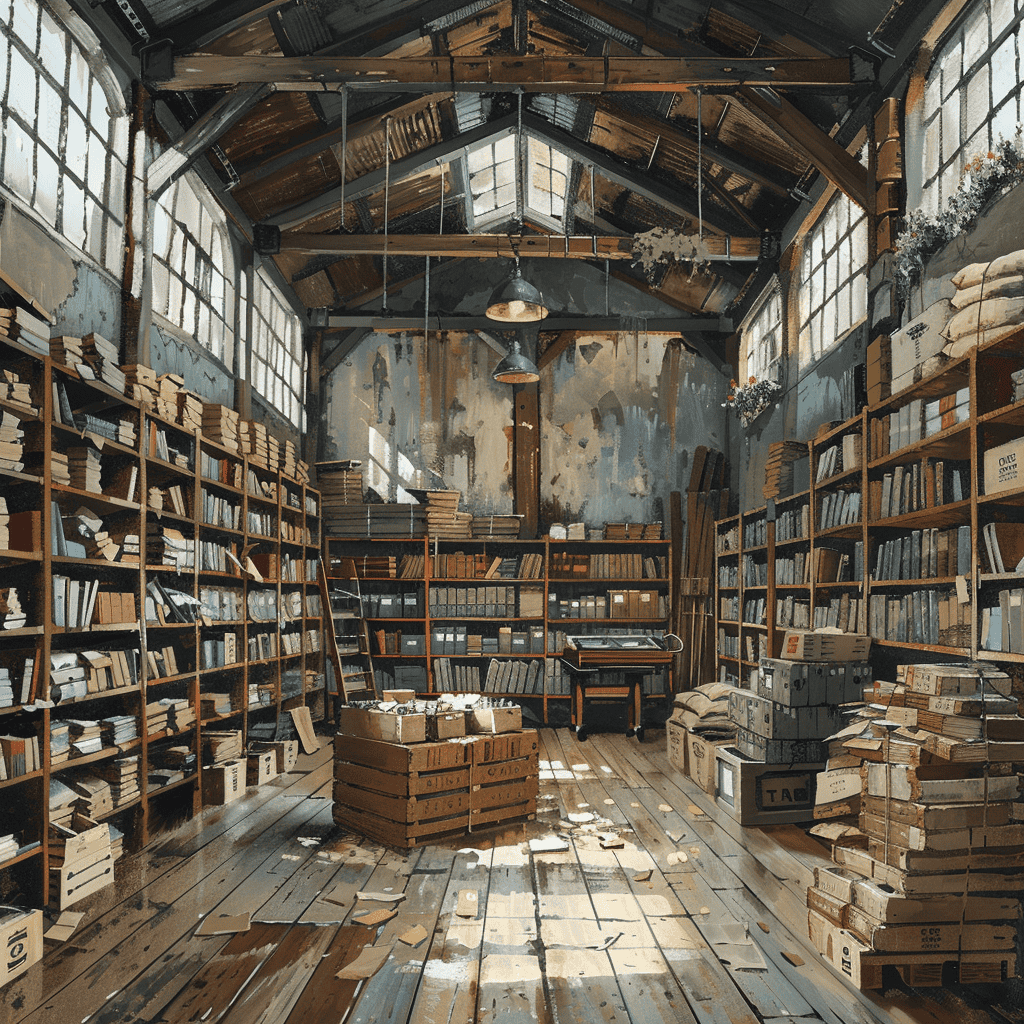
Warehouse Location
Warehouses are typically located near manufacturing sites or demand centers to facilitate the storage and distribution of goods. Their locations are often chosen based on proximity to production facilities or areas with high demand.
Distribution Center Location
Distribution centers are strategically positioned for logistics efficiency, often near major transport hubs such as highways, airports, and seaports. This placement allows for quicker distribution of goods to various destinations.
Technology and Automation
Technology and automation play significant roles in the operations of both warehouses and distribution centers, enhancing their efficiency and accuracy.
Warehouse Technology
Warehouses employ technologies like barcode scanning, RFID, and Warehouse Management Systems (WMS) to manage inventory and operations efficiently.
- Barcode Scanning: Helps in tracking and managing inventory accurately.
- RFID: Radio Frequency Identification for improved inventory visibility and accuracy.
- Warehouse Management Systems (WMS): Software that helps in optimizing warehouse operations, from receiving to shipping.
Distribution Center Technology
Distribution centers use advanced automation technologies like automated storage and retrieval systems (AS/RS), conveyor systems, and real-time tracking to streamline operations and improve efficiency.

- Automated Storage and Retrieval Systems (AS/RS): Automates the placement and retrieval of goods, increasing efficiency.
- Conveyor Systems: Facilitate the movement of goods within the distribution center.
- Real-Time Tracking: Provides up-to-date information on inventory and order status.
Cost Considerations
Cost considerations for warehouses and distribution centers involve various factors, including operational and technological investments.
Warehouse Costs
Warehouses incur expenses for rent, utilities, labor, and inventory carrying costs. These costs are generally lower than those of distribution centers due to simpler operations.
Distribution Center Costs
Distribution centers face higher operational costs due to advanced technologies, higher labor requirements, and greater complexity in operations. Investments in automation and technology also add to the costs.
Benefits and Drawbacks
Each facility type has its own set of benefits and drawbacks, which can influence a business’s decision based on its needs.
Warehouse Benefits
Warehouses offer large storage capacity and lower operating costs, making them ideal for long-term storage needs.
Warehouse Drawbacks
Warehouses have slower response times and less flexibility, which can be a disadvantage in fast-moving industries.
Distribution Center Benefits
Distribution centers provide faster delivery times and greater flexibility, allowing businesses to respond quickly to market demands and customer orders.
Distribution Center Drawbacks
Distribution centers have higher costs and complex operations, which can be challenging to manage without significant investment in technology and skilled labor.
Warehouse vs Distribution Center Examples
Real-world examples and case studies illustrate how warehouses and distribution centers operate and highlight their respective advantages and challenges.
Warehouse Examples
Examples include cold storage warehouses and bulk storage facilities, which are essential for industries requiring long-term preservation of goods, such as food and pharmaceuticals.
Distribution Center Examples
Examples include Amazon fulfillment centers and retail distribution hubs, which are designed to handle large volumes of orders efficiently and quickly.