Warehouse bays are crucial for optimizing storage, ensuring efficient inventory management, and maintaining safety standards. This article provides an in-depth exploration of what is a bay in a warehouse, the definition, types, design, usage, benefits, and safety considerations of warehouse bays. Understanding these aspects is essential for effective warehouse layout evaluation.
What is a Bay in a Warehouse: Definition and Purpose
A bay in a warehouse is a designated area between two columns or supports, specifically allocated for the storage of goods and materials. It serves as a fundamental unit of organization within the warehouse, facilitating systematic storage and retrieval. Bays can vary in size and configuration, depending on the specific needs of the warehouse and the type of goods being stored.
Organizing Storage Space
Bays segment the warehouse into manageable sections, making it easier to categorize and store various goods. By dividing the storage area into distinct zones, bays help maintain order and prevent the clutter that can arise in unstructured storage environments. This organization simplifies the process of locating and retrieving items, enhancing overall efficiency.
Facilitating Easy Access
Properly arranged bays ensure that items can be accessed quickly and efficiently, reducing retrieval times. The strategic layout of bays allows workers to navigate the warehouse with ease, minimizing the time spent searching for products. This ease of access is particularly important in high-volume warehouses where speed and accuracy are critical.
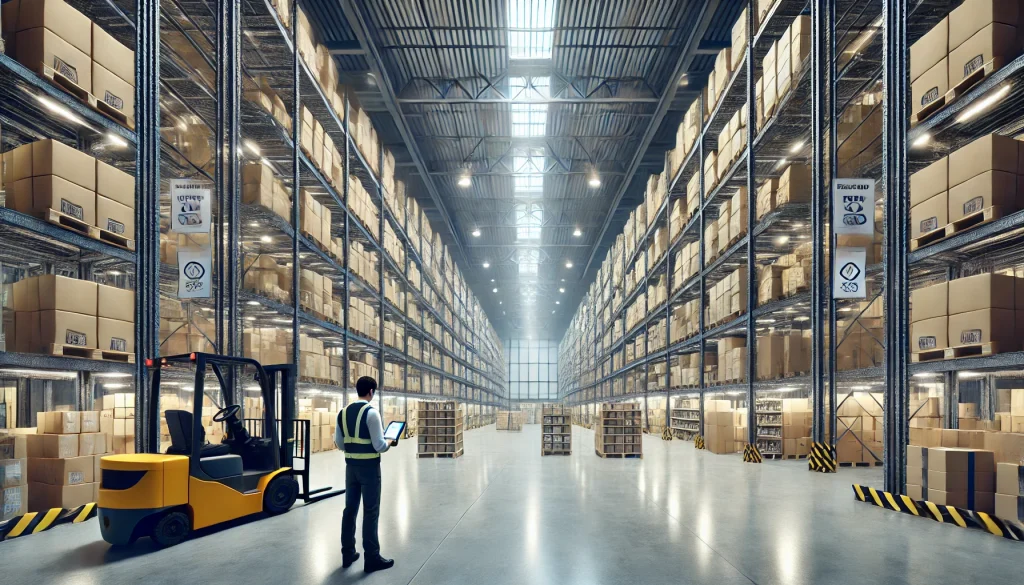
Improving Inventory Management
Clearly defined bays enhance the accuracy of inventory tracking and stock control, ensuring better oversight of goods. By assigning specific locations to each type of product, warehouses can maintain precise records of stock levels, reducing the likelihood of errors. This organized approach also aids in conducting regular inventory audits and identifying discrepancies.
Types of Bays
Different types of bays serve varying storage needs, from maximizing accessibility to increasing storage density. Understanding the types of bays available can help in selecting the most appropriate configuration for a warehouse’s specific requirements.
Single-Deep Bays
Single-deep bays store one pallet deep, providing direct access to each pallet. They are ideal for warehouses that require high accessibility and quick retrieval times. These bays are often used in environments where a wide variety of items are stored, and fast picking is essential. The simplicity of single-deep bays makes them easy to manage and reduces the need for specialized equipment.
Double-Deep Bays
Double-deep bays store two pallets deep, increasing storage density. However, accessing the second row of pallets requires specialized equipment, such as deep-reach forklifts. While this configuration reduces immediate accessibility, it offers a balance between space utilization and accessibility. Double-deep bays are suitable for storing large quantities of similar items that do not require frequent access.
Push-Back Bays
Push-back bays utilize a rail system allowing multiple pallets to be stored deep, accessed from one side. This system maximizes storage density while maintaining reasonable access efficiency. Pallets are placed on nested carts that move along inclined rails, allowing each pallet to be pushed back when a new one is added. This type of bay is beneficial for warehouses with limited floor space, as it allows for high-density storage without compromising accessibility.
Drive-In Bays
Drive-in bays allow forklifts to drive into the bay to store multiple pallets deep, accessed from only one side. This method is suitable for storing large quantities of similar products, such as seasonal items or bulk materials. While drive-in bays offer high storage density, they require careful planning to avoid blocking access to items stored deeper within the bay. This type of storage is best used for items with low turnover rates.
Flow-Through Bays
Flow-through bays use gravity roller tracks for first-in, first-out (FIFO) inventory rotation. These bays are essential for managing perishable goods or products with expiration dates, ensuring that older stock is used before newer stock. Flow-through bays are commonly found in industries such as food and beverage, pharmaceuticals, and retail. The gravity-based system reduces manual handling and ensures a consistent flow of goods through the warehouse.
Design and Layout
The design and layout of warehouse bays significantly impact their efficiency and functionality. Key factors such as column spacing, racking systems, aisle widths, load capacity, and vertical space utilization must be considered to optimize storage solutions.
Column Spacing
The spacing between columns determines the width of the bay, influencing storage capacity and accessibility. Proper column spacing is critical for maximizing space utilization while ensuring structural stability. Columns must be strategically placed to support the weight of stored materials and accommodate the movement of forklifts and other equipment. The goal is to balance storage density with ease of access, ensuring that workers can efficiently navigate the warehouse.
Racking Systems
Various racking systems can be used within bays, including pallet racking, cantilever racking, and mezzanine floors. Pallet racking is the most common system, providing flexible storage for a wide range of goods. Cantilever racking is ideal for storing long or bulky items, such as pipes and lumber, while mezzanine floors add additional levels of storage within the same footprint. Each system has its advantages, depending on the type of goods stored and the desired accessibility. The choice of racking system should align with the warehouse’s operational needs and storage requirements.
Aisle Widths
The width of aisles between bays affects the maneuverability of forklifts and other picking equipment. Wider aisles improve accessibility but reduce overall storage space. Narrow aisles, on the other hand, increase storage density but require specialized narrow-aisle forklifts to navigate. The optimal aisle width depends on the balance between storage efficiency and operational ease. Consideration must be given to the types of equipment used and the volume of traffic within the warehouse.
Load Capacity
Each bay must be designed to handle the weight and volume of the stored materials. Overloading bays can lead to structural failures and safety hazards. It’s essential to adhere to the load limits specified by the racking system manufacturers and conduct regular inspections to ensure compliance. Proper load distribution within the bays prevents uneven stress on the structure, enhancing safety and longevity.
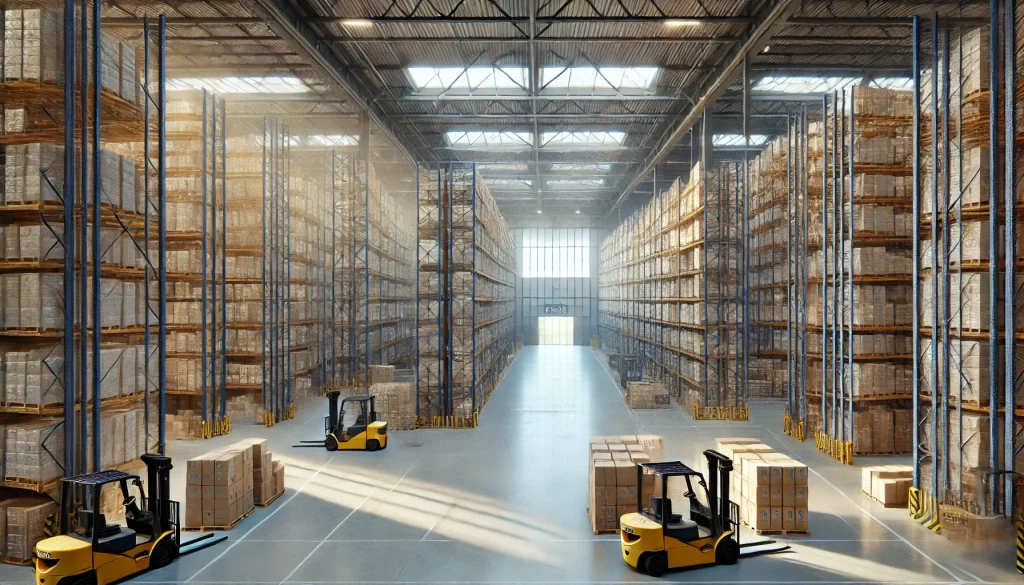
Vertical Space Utilization
Maximizing the height of bays increases storage capacity. High bay racking systems allow warehouses to utilize vertical space effectively, reducing the footprint required for storage. Vertical space utilization is particularly important in warehouses with limited floor area. Using automated systems, such as vertical lift modules or automated storage and retrieval systems (AS/RS), can further enhance the use of vertical space while improving efficiency.
Usage and Applications
Warehouse bays have diverse applications, from managing inventory to fulfilling orders and storing bulk materials. Their usage extends across various industries, each with specific requirements and challenges.
Inventory Management
Organized bays facilitate accurate inventory tracking and stock control, making it easier to monitor and manage goods. By assigning specific locations to each type of product, warehouses can maintain precise records of stock levels, reducing the likelihood of errors. This organized approach also aids in conducting regular inventory audits and identifying discrepancies, ensuring that stock levels are accurate and up-to-date.
Order Picking
An efficient layout of bays supports quicker and more accurate order fulfillment, improving overall warehouse productivity. By strategically positioning high-demand items in easily accessible bays, warehouses can reduce picking times and increase throughput. The use of technology, such as barcode scanning and warehouse management systems (WMS), further enhances the accuracy and speed of order picking.
Bulk Storage
Bays are used for storing large quantities of homogeneous products, ensuring that bulk items are easily accessible and organized. Bulk storage bays are typically designed to accommodate high-volume items that do not require frequent access. This method of storage is commonly used in industries such as manufacturing, where raw materials or finished products are stored in large quantities.
Cold Storage
Bays designed for temperature-controlled environments are essential for storing perishable goods, such as food and pharmaceuticals. Cold storage bays must maintain consistent temperatures to preserve the quality and safety of the products. Specialized racking systems and insulation materials are used to ensure that temperature-sensitive items are stored under optimal conditions. Properly designed cold storage bays prevent spoilage and extend the shelf life of perishable goods.
Automated Storage and Retrieval Systems (AS/RS)
Bays integrated with automation enhance high-speed storage and retrieval, reducing manual labor and increasing efficiency. AS/RS use automated machinery to store and retrieve items from bays, minimizing the need for human intervention. These systems are particularly useful in high-volume warehouses where speed and accuracy are critical. Automation reduces the risk of errors, increases storage density, and improves overall operational efficiency.
Benefits and Efficiency
The implementation of well-designed warehouse bays offers numerous benefits, from optimizing space utilization to improving safety and scalability.
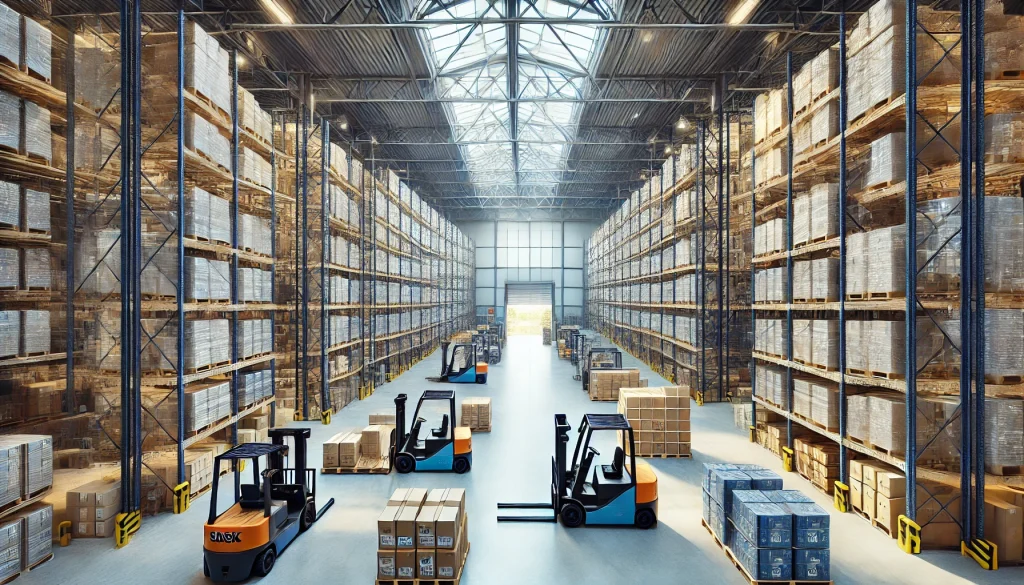
Optimized Space Utilization
Bays maximize storage capacity within the available warehouse space, ensuring that every square foot is used effectively. By organizing goods into specific bays, warehouses can reduce wasted space and increase storage density. This optimization allows businesses to store more products within the same footprint, reducing the need for additional storage facilities.
Improved Accessibility
Organized bays allow for easy access to goods, reducing retrieval time and improving operational efficiency. Workers can quickly locate and retrieve items, minimizing downtime and increasing productivity. Improved accessibility also enhances the ability to respond to customer orders and demands promptly.
Enhanced Organization
Clearly defined bays improve overall warehouse organization and workflow, making it easier to locate and manage items. An organized warehouse reduces the likelihood of misplaced or lost items, ensuring that products are readily available when needed. This enhanced organization streamlines operations and supports efficient inventory management.
Increased Safety
Properly designed bays reduce the risk of accidents and damage to goods, contributing to a safer work environment. By adhering to load limits and maintaining clear aisles, warehouses can minimize the risk of structural failures and collisions. Safety features, such as rack guards and safety netting, further protect workers and goods.
Scalability
Bays can be reconfigured to accommodate changing storage needs and inventory volumes, providing flexibility for business growth. As demand fluctuates, warehouses can adjust the layout and design of bays to optimize storage capacity and efficiency. This scalability ensures that warehouses can adapt to evolving business requirements without significant disruptions.
Safety and Compliance
Ensuring the safety and compliance of warehouse bays is essential for protecting workers, goods, and the overall integrity of the storage system.
Safety Standards
Adherence to OSHA and other regulatory standards for warehouse safety is crucial. Bays must be designed and maintained to meet these standards, ensuring a safe working environment. Regular safety audits and training programs help reinforce compliance and promote a culture of safety within the warehouse.
Load Limits
Ensuring that bays are not overloaded beyond their designed capacity is essential to prevent structural failures and ensure safety. Load limits should be clearly marked and communicated to all warehouse personnel. Regular inspections and monitoring help identify potential overloading issues before they become hazards.
Fire Safety
Proper spacing and layout of bays are necessary to comply with fire safety regulations, including the provision of adequate fire exits and suppression systems. Fire safety measures, such as sprinkler systems and fire-resistant materials, help mitigate the risk of fire and protect both workers and goods.
Ergonomics
Designing bays to minimize strain on workers during material handling reduces the risk of injuries and improves overall productivity. Ergonomic considerations, such as the height of storage levels and the use of lifting aids, enhance worker comfort and reduce the likelihood of musculoskeletal disorders.
Maintenance
Regular inspection and maintenance of bays are required to ensure their structural integrity and safety. This includes checking for damage, wear, and compliance with safety standards. Preventive maintenance programs help identify and address potential issues before they lead to costly repairs or accidents.