Warehouses are pivotal to the global supply chain, serving as the backbone for storing, managing, and distributing goods. This comprehensive article delves into the various aspects of warehouses, exploring their functions, types, operational processes, and their critical role in logistics and supply chain management. Understanding these elements is crucial for effective warehouse layout evaluation.
Purpose and Function of Warehouses
Warehouses serve several essential functions that ensure the smooth operation of supply chains:
Storage
The primary function of a warehouse is to provide space for storing goods. This includes raw materials waiting for production, work-in-progress items during manufacturing, and finished products ready for distribution. Efficient storage helps businesses maintain a steady supply of goods to meet customer demands.
Types of Storage Solutions
Warehouses employ various storage solutions such as shelving, pallet racking, and automated storage and retrieval systems (AS/RS). These solutions optimize space utilization and ensure easy access to stored items.
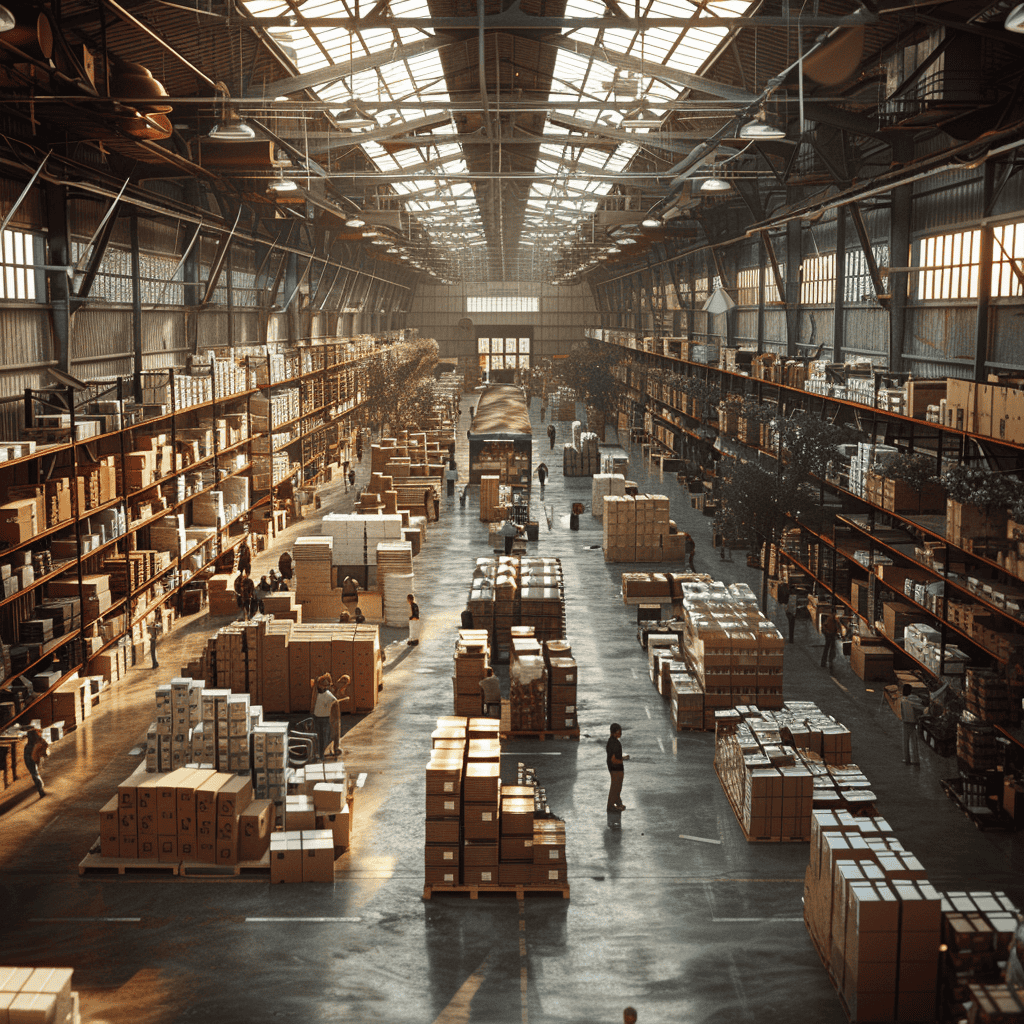
Benefits of Proper Storage
Proper storage helps maintain product quality, prevent damage, and ensure compliance with regulatory standards. It also facilitates inventory control and quick retrieval of items.
Distribution
Warehouses act as hubs for distribution, where goods are received from suppliers, sorted, and then dispatched to their next destination, whether that’s retail stores, direct customers, or other businesses. This distribution role is critical for ensuring timely delivery and maintaining product availability.
Distribution Strategies
Effective distribution strategies include cross-docking, where incoming goods are directly transferred to outbound vehicles, and zone picking, where the storage hub is divided into zones with specific picking responsibilities.
Role in Supply Chain
Distribution centers play a key role in reducing delivery times, lowering transportation costs, and ensuring that products reach customers promptly and in good condition. These facilities serve as central points in the supply chain where goods are received from suppliers, stored temporarily, and then distributed to their final destinations. By strategically locating distribution centers near major transportation routes and customer bases, businesses can optimize their logistics operations, minimize delays, and improve overall efficiency.
Inventory Management
Effective inventory management within a warehouse ensures that stock levels are accurately tracked and maintained. This involves sophisticated systems to monitor inventory, prevent overstocking or stockouts, and optimize the replenishment process.
Inventory Tracking Systems
Modern warehouses use barcode scanning, RFID technology, and inventory management software to keep real-time records of inventory levels and locations.
Inventory Control Techniques
Techniques such as ABC analysis, just-in-time (JIT) inventory, and cycle counting help in maintaining optimal inventory levels and minimizing holding costs.
Types of Warehouses
There are several types of warehouses, each designed to meet specific needs and operational requirements:
Private Warehouses
Private warehouses are owned and operated by a single company for storing its own goods. These facilities offer greater control over storage and distribution processes, which can lead to increased efficiency and cost savings for the owning company.
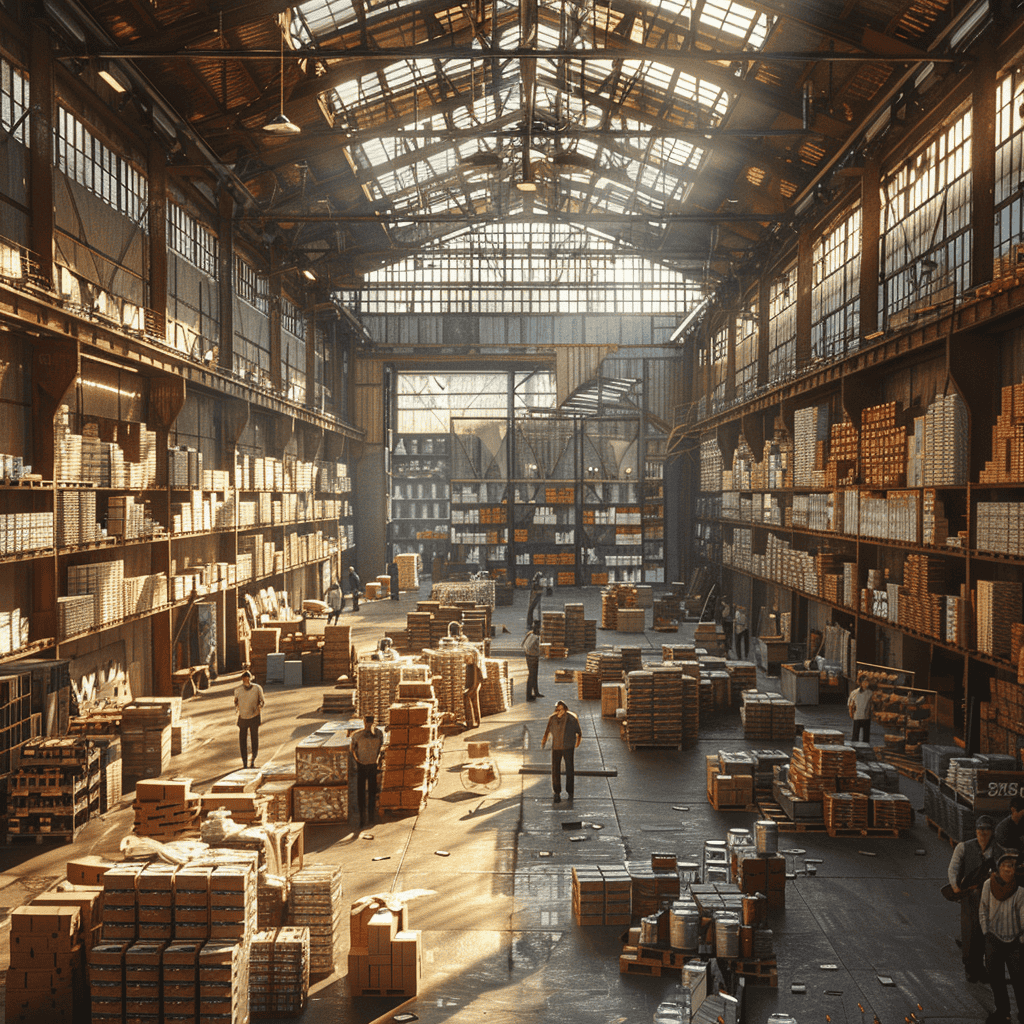
Advantages of Private Warehouses
Private warehouses provide tailored solutions, greater control over operations, and enhanced security for stored goods. They also allow companies to customize storage conditions to their specific needs.
Considerations for Private Warehouses
Owning and operating a private warehouse requires significant capital investment and ongoing maintenance costs. Companies need to consider these factors when deciding between private and public warehousing options.
Public Warehouses
Third-party logistics providers operate public warehouses and are available for rent by multiple businesses. They offer flexibility and scalability, allowing companies to adjust their storage space according to fluctuating demands without the need for significant capital investment.
Benefits of Public Warehouses
Public warehouses provide cost-effective storage solutions, flexible space options, and access to advanced logistics services without the need for large upfront investments.
Limitations of Public Warehouses
While public warehouses offer flexibility, they may also present challenges in terms of control over storage conditions and potential conflicts with other clients sharing the space.
Automated Warehouses
Automated warehouses utilize robotics and advanced automation systems to handle storage and retrieval tasks. These facilities are designed for high efficiency and precision, reducing labor costs and minimizing errors in inventory management.
Automation Technologies
Technologies used in automated warehouses include automated guided vehicles (AGVs), conveyor systems, robotic arms, and automated storage and retrieval systems (AS/RS).
Benefits of Automation
Automation increases operational efficiency, reduces human error, and lowers labor costs. It also enables faster order processing and improved accuracy in inventory management.
Climate-Controlled Warehouses
Climate-controlled warehouses are equipped to maintain specific temperature and humidity levels, making them ideal for storing perishable or sensitive goods such as food, pharmaceuticals, and electronics.
Types of Climate Control
Climate-controlled warehouses can be classified into refrigerated warehouses (for cold storage), humidity-controlled warehouses, and warehouses with both temperature and humidity controls. Each type is designed to maintain the quality and safety of different types of goods.
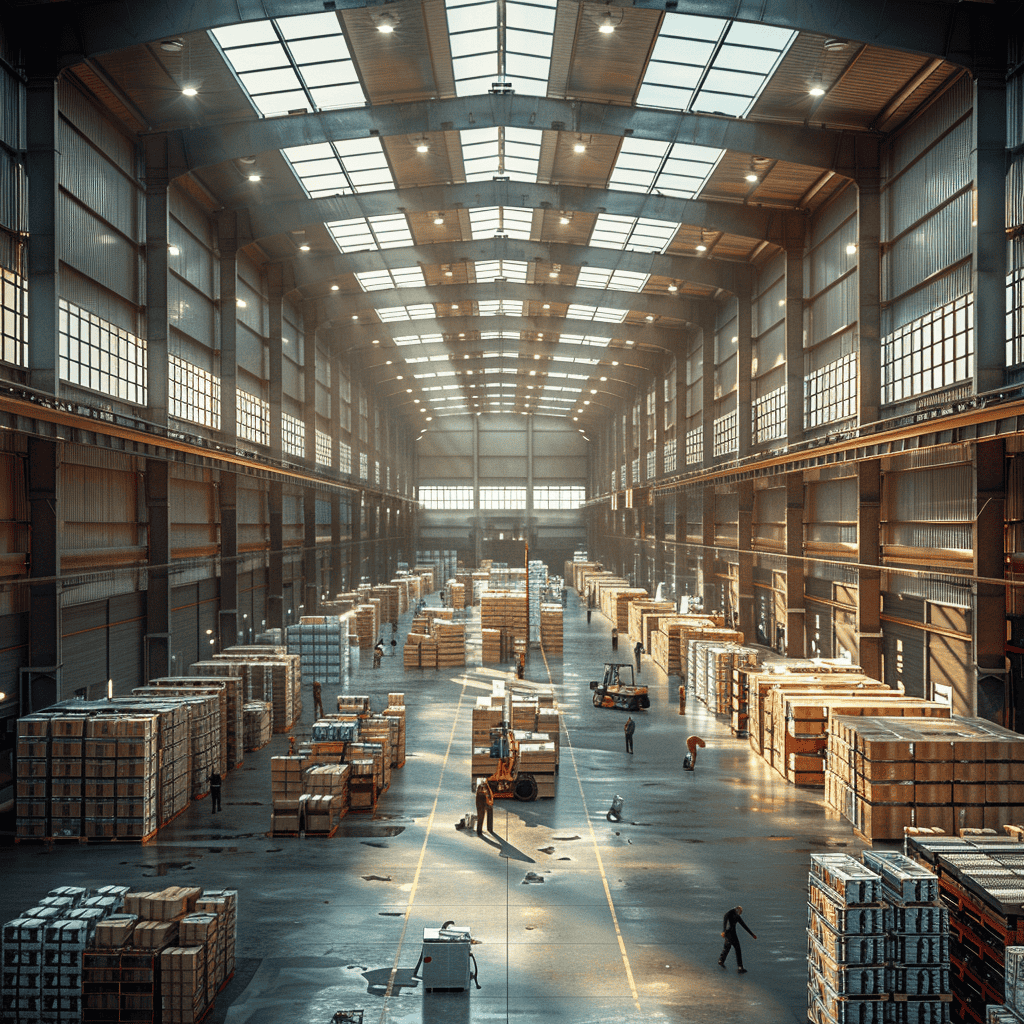
Importance of Climate Control
Maintaining the appropriate climate within a warehouse prevents spoilage, degradation, and contamination of sensitive products. It also ensures compliance with health and safety regulations for products like food and pharmaceuticals.
Components and Layout of a Warehouse
The design and layout of a warehouse are crucial for optimizing storage space and ensuring efficient operations. Key components include:
Receiving Area
The receiving area is where goods are delivered to the warehouse. Here, items are inspected, verified against purchase orders, and logged into the inventory system. Efficient receiving processes are vital for accurate inventory management and timely distribution.
Receiving Procedures
Receiving procedures include unloading goods, checking for damages, verifying quantities against purchase orders, and entering data into inventory management systems.
Challenges in Receiving
Challenges include handling large volumes of incoming goods, ensuring accuracy in data entry, and coordinating with suppliers to schedule deliveries efficiently.
Storage Area
The storage area is where goods are kept until they are needed. This area can include various storage solutions such as shelving, racks, and pallets. Effective organization in the storage area ensures easy access and maximizes space utilization.
Storage Methods
Common storage methods include pallet racking for bulk items, shelving for smaller items, and automated storage and retrieval systems (AS/RS) for high-density storage.
Space Utilization
Maximizing space utilization involves optimizing the layout of storage racks, minimizing aisle widths, and using vertical space efficiently. This also includes strategic placement of frequently accessed items.
Picking Area
The picking area is designated for retrieving items needed for customer orders. Efficient picking processes are essential for quick order fulfillment and minimizing errors. Technologies like barcode scanners and pick-to-light systems can enhance picking accuracy and speed.
Picking Techniques
Techniques include batch picking, where multiple orders are picked simultaneously; zone picking, where pickers are assigned to specific areas; and wave picking, which coordinates picking schedules with shipping schedules.
Tools for Picking
Tools such as barcode scanners, RFIDs, and voice-picking systems help improve accuracy and efficiency in the picking process. Automated guided vehicles (AGVs) can also assist in moving picked items to the packing area.
Packing Area
In the packing area, items selected for orders are packaged securely for shipment. This area is equipped with packing materials and tools to ensure that goods are protected during transit.
Packing Materials
Materials used for packing include boxes, bubble wrap, packing peanuts, and pallets. Choosing the right materials is essential to protect goods from damage during transit.
Packing Procedures
Packing procedures involve verifying picked items, using appropriate packing materials, sealing packages securely, and labeling them accurately for shipping.
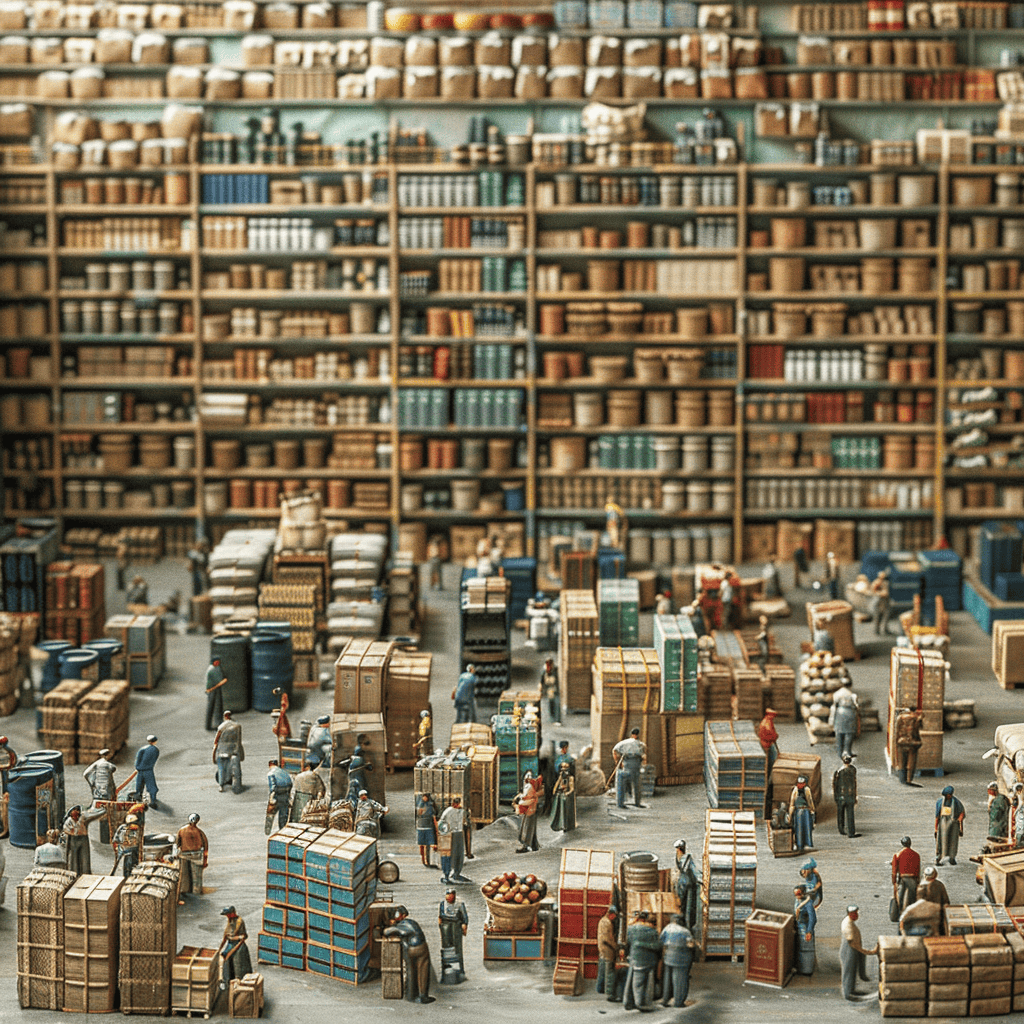
Shipping Area
The shipping area is where packed orders are prepared for dispatch. This includes labeling, weighing, and loading goods onto transportation vehicles. Efficient shipping processes ensure timely delivery and customer satisfaction.
Shipping Preparation
Preparation involves printing shipping labels, weighing packages to determine shipping costs, and organizing packages based on delivery routes and priorities.
Challenges in Shipping
Challenges include coordinating with carriers, managing shipping schedules, and handling last-minute changes or delays in transportation.
Warehouse Management Systems (WMS)
Warehouse management systems (WMS) are software solutions designed to optimize warehouse operations. Key features of a WMS include:
Inventory Tracking
A WMS provides real-time tracking of inventory levels and locations within the warehouse. This helps prevent stockouts and overstock situations, ensuring that the right products are available when needed.
Tracking Technologies
Technologies such as barcode scanning, RFID, and GPS tracking are commonly used in WMS to monitor the movement and location of goods within the warehouse.
Benefits of Inventory Tracking
Effective inventory tracking improves accuracy in stock management, reduces shrinkage, and enhances the ability to meet customer demands promptly.
Order Fulfillment
WMS systems manage the picking, packing, and shipping of orders, streamlining the fulfillment process. This leads to faster order processing times and improved accuracy.
Fulfillment Strategies
Strategies include wave picking, cross-docking, and drop shipping, each designed to optimize the speed and efficiency of order fulfillment.
Role of WMS in Fulfillment
A WMS coordinates the various stages of order fulfillment, ensuring that orders are processed quickly, accurately, and efficiently. It also provides real-time updates on order status.
Efficiency Optimization
Advanced WMS solutions offer tools to optimize warehouse layout and processes. This includes analyzing traffic patterns, storage methods, and labor allocation to maximize efficiency and reduce operational costs.
Layout Optimization
Layout optimization involves designing the warehouse floor plan to minimize travel time, reduce bottlenecks, and ensure smooth workflow. This may include adjusting aisle widths, storage locations, and workflow patterns.
Process Improvement
WMS can help identify inefficiencies in warehouse operations and suggest improvements, such as reorganizing storage areas, adjusting picking routes, and reallocating labor resources.
Operational Processes in a Warehouse
The daily operations in a warehouse involve several key processes:
Receiving
Receiving involves inspecting and logging incoming goods. This step ensures that the correct items are delivered and that they meet quality standards.
Inspection and Verification
Goods are inspected for damage, checked against purchase orders, and verified for quantity and quality. This process ensures that only acceptable items are entered into inventory.
Data Entry
Accurate data entry is crucial for maintaining up-to-date inventory records. This involves scanning barcodes, entering item details, and updating inventory management systems.
Putaway
Putaway is the process of moving received goods to their designated storage locations. Efficient putaway systems improve space utilization and make it easier to find items when needed.
Putaway Strategies
Strategies include directed putaway, where the WMS suggests optimal storage locations, and random putaway, where goods are stored in any available space and tracked by the system.
Benefits of Efficient Putaway
Efficient putaway reduces handling time, minimizes errors, and improves overall warehouse productivity. It also ensures that items are stored in appropriate conditions.
Picking
Picking involves retrieving items for customer orders from their storage locations. Effective picking processes are crucial for timely order fulfillment and minimizing errors.
Picking Methods
Methods include single-order picking, where each order is picked individually, and batch picking, where multiple orders are picked simultaneously to save time.
Tools and Technologies
Tools such as pick-to-light systems, voice-directed picking, and mobile devices enhance picking accuracy and efficiency. Automated solutions like AGVs can also assist in picking operations.
Packing
In the packing process, items are securely packaged for shipment. This includes selecting appropriate packaging materials and ensuring that goods are protected during transit.
Packing Techniques
Techniques include void fill, where empty spaces in packages are filled to prevent movement, and double boxing for extra protection of fragile items.
Quality Control
Quality control checks ensure that the correct items are packed, packaging is secure, and labels are accurate. This step helps prevent shipping errors and customer dissatisfaction.
Shipping
The shipping process involves preparing and dispatching orders for delivery. This includes labeling, weighing, and loading goods onto transportation vehicles. Efficient shipping processes ensure timely delivery and customer satisfaction.
Coordination with Carriers
Effective coordination with carriers is essential for timely pickups and deliveries. This includes scheduling pickups, preparing shipping documents, and tracking shipments.
Managing Delays
Warehouses must be prepared to handle delays and disruptions in the shipping process. This includes having contingency plans, communicating with customers, and working with carriers to resolve issues.
Importance of Warehouses in Supply Chain Management
Warehouses play a vital role in the supply chain, providing several benefits:
Buffer Against Demand Fluctuations
Warehouses help manage fluctuations in demand and supply, ensuring that products are available to meet customer needs. This buffer stock prevents disruptions in the supply chain and enhances reliability.
Managing Inventory Levels
Maintaining buffer stock levels helps businesses respond quickly to changes in demand, avoiding stockouts and lost sales. It also allows for smoother production schedules.
Enhancing Supply Chain Resilience
Buffer stocks increase the resilience of the supply chain by providing a cushion against supply chain disruptions, such as delays in transportation or production issues.
Cost Efficiency
Centralized storage in warehouses reduces transportation costs by enabling bulk shipping and minimizing the need for frequent deliveries. This leads to significant cost savings for businesses.
Economies of Scale
Warehouses allow businesses to take advantage of economies of scale by purchasing and storing goods in bulk, reducing per-unit costs.
Reducing Logistics Costs
By consolidating shipments and optimizing transportation routes, warehouses help reduce overall logistics costs, making supply chain operations more cost-effective.
Improved Customer Service
Efficient warehouse operations ensure faster order fulfillment and delivery times. This improves customer satisfaction and helps businesses maintain a competitive edge.
Faster Order Fulfillment
Efficient picking, packing, and shipping processes ensure that orders are processed and delivered quickly, meeting customer expectations for fast service.
Enhanced Accuracy
Accurate inventory management and order processing reduce the likelihood of errors, ensuring that customers receive the correct items in good condition.
Challenges and Trends in Warehousing
The warehousing industry faces several challenges and is also witnessing emerging trends:
Space Utilization
Maximizing storage capacity while maintaining accessibility is a constant challenge. Innovative storage solutions and efficient layout designs are essential for optimal space utilization.
Vertical Storage
Using vertical space with high-rise racking systems and mezzanine floors can significantly increase storage capacity without expanding the warehouse footprint.
Dynamic Storage Systems
Dynamic storage systems, such as mobile racking and flow racks, enhance space utilization by allowing flexible storage configurations based on inventory needs.
Technology Integration
The integration of advanced technologies such as artificial intelligence (AI), Internet of Things (IoT), and robotics is transforming warehouse operations. These technologies enhance efficiency, accuracy, and overall productivity.
AI and Machine Learning
AI and machine learning algorithms analyze warehouse data to optimize processes, predict demand, and improve decision-making. These technologies help in inventory forecasting, labor management, and route optimization.
IoT and Smart Warehousing
IoT devices and sensors provide real-time data on inventory levels, equipment status, and environmental conditions. Smart warehousing enables proactive maintenance, efficient resource utilization, and better inventory management.
Sustainability
There is a growing focus on sustainability in warehousing. This includes implementing eco-friendly practices such as energy-efficient lighting, waste reduction, and the use of renewable energy sources.
Green Building Practices
Adopting green building practices, such as using sustainable materials, optimizing energy use, and installing solar panels, helps reduce the environmental impact of warehouses.
Waste Reduction
Implementing recycling programs, reducing packaging waste, and minimizing energy consumption are key strategies for improving sustainability in warehousing operations.
Conclusion
Warehouses are an indispensable component of modern supply chains. They facilitate the efficient storage, management, and distribution of goods, ensuring that products are available to meet market demands. By understanding the various aspects of warehousing, businesses can optimize their operations, reduce costs, and improve customer satisfaction. As technology continues to evolve, the future of warehousing promises even greater efficiency and innovation.