Putaway is a critical aspect of warehouse operations that directly impacts efficiency, accuracy, and overall productivity. This article explains what is putaway in warehouse, the definition, importance, strategies, technologies, process steps, challenges, best practices, metrics, and the impact of putaway on warehouse efficiency.
What is Putaway in Warehouse
Understanding what putaway entails and its importance sets the foundation for optimizing warehouse operations.
Definition: Putaway refers to the process of moving received goods to their designated storage locations within a warehouse. This involves several steps, including receiving, transporting, and storing items organizationally.
Importance: Effective putaway ensures that inventory is systematically organized, easily accessible, and accurately tracked. It improves warehouse efficiency by reducing retrieval times, enhancing inventory accuracy, maximizing space utilization, and maintaining a safe working environment. Proper putaway practices also help minimize damage to goods and streamline subsequent warehouse processes like picking and shipping.
Putaway Strategies
Employing different putaway strategies can significantly impact the efficiency and organization of a warehouse.
Fixed Location
In this strategy, each item has a predetermined storage location. While it simplifies the retrieval process and ensures a consistent place for each item, it may not make the best use of available storage space.
Random Location
Items are placed in any available space, with locations managed by a Warehouse Management System (WMS) to optimize space usage. This strategy is more flexible and can lead to better space utilization but requires robust tracking systems to maintain organization.
Zone-Based
Items are stored in specific zones based on characteristics like size, weight, or temperature requirements. This strategy balances efficiency and organization, making it easier to manage items with similar storage needs.
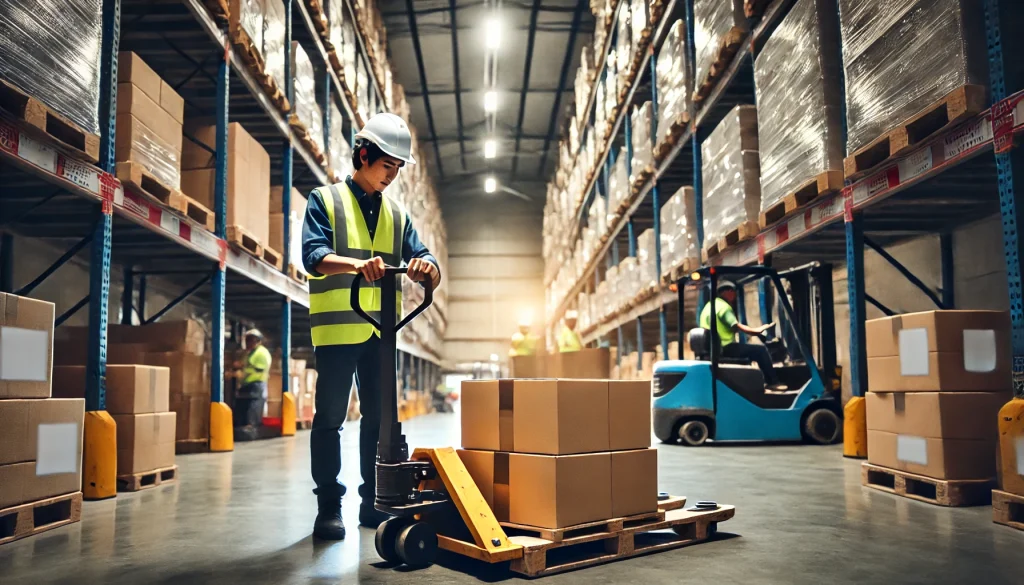
Dynamic Slotting
Storage locations are dynamically assigned based on real-time data. This approach optimizes space usage and improves retrieval efficiency by continuously adapting to changing inventory levels and storage needs.
Technologies Used
Advanced technologies play a crucial role in enhancing the efficiency and accuracy of the putaway process.
Warehouse Management System (WMS)
A WMS centralizes and automates warehouse operations, including putaway. It enhances efficiency and accuracy by managing inventory, tracking item locations, and optimizing storage layouts.
RFID Technology
Radio Frequency Identification (RFID) uses radio waves to identify and track items in real-time. This technology improves inventory management by providing accurate, up-to-date information on item locations and statuses.
Barcode Scanning
Barcode scanning facilitates accurate data entry and tracking during the putaway process. Each item or pallet is labeled with a barcode, which is scanned to update the WMS with its location and other details.
Automated Guided Vehicles (AGVs)
AGVs automate the transportation of goods within the warehouse, reducing the need for manual labor and increasing efficiency. These vehicles follow predefined paths and can be integrated with the WMS for seamless operations.
Voice-Directed Systems
Voice-directed systems provide verbal instructions to workers, streamlining the putaway process and reducing errors. Workers receive real-time directions via headsets, allowing for hands-free operation and improved productivity.
Putaway Process Steps
The putaway process involves several key steps that ensure goods are stored accurately and efficiently.
Receiving
The first step in the putaway process is receiving the goods. This involves inspecting and verifying the received items against purchase orders for quantity and quality. Documentation is also updated in the WMS to reflect the receipt of goods.
Data Entry
Accurate data entry is crucial for maintaining inventory accuracy. The details of the received goods, including quantities and storage requirements, are recorded in the WMS.
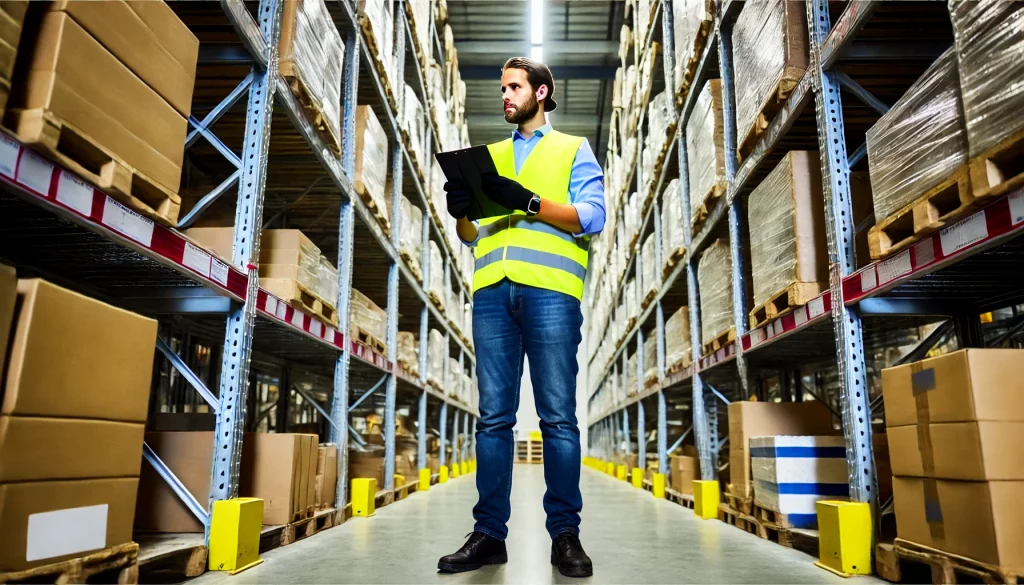
Sorting
Items are sorted based on their storage requirements or designated zones. Sorting ensures that similar items are grouped together, facilitating easier storage and retrieval.
Transporting
The sorted items are then transported to their designated storage locations. Appropriate equipment, such as forklifts or conveyors, is used to move the items efficiently.
Storing
Finally, items are placed in their designated storage locations. Proper organization during this step ensures that items are easily accessible and that storage space is optimized.
Challenges and Solutions
Addressing common challenges in the putaway process is essential for maintaining an efficient warehouse operation.
Space Utilization
Challenge: Efficiently utilizing available storage space can be challenging, especially in high-density warehouses.
Solution: Implement dynamic slotting and regularly review storage layouts to maximize space usage.
Labor Efficiency
Challenge: Maintaining high labor efficiency while ensuring accuracy can be difficult.
Solution: Use automation technologies like AGVs and voice-directed systems, and provide regular training to warehouse staff.
Inventory Accuracy
Challenge: Ensuring accurate inventory records is critical for efficient warehouse operations.
Solution: Utilize RFID technology and barcode scanning to maintain real-time, accurate inventory data.
Traffic Management
Challenge: Managing the flow of goods and equipment within the warehouse to avoid congestion and delays.
Solution: Design efficient warehouse layouts and implement automated systems to streamline movement and reduce congestion.
Best Practices
Implementing best practices in the putaway process can significantly enhance warehouse performance and efficiency.
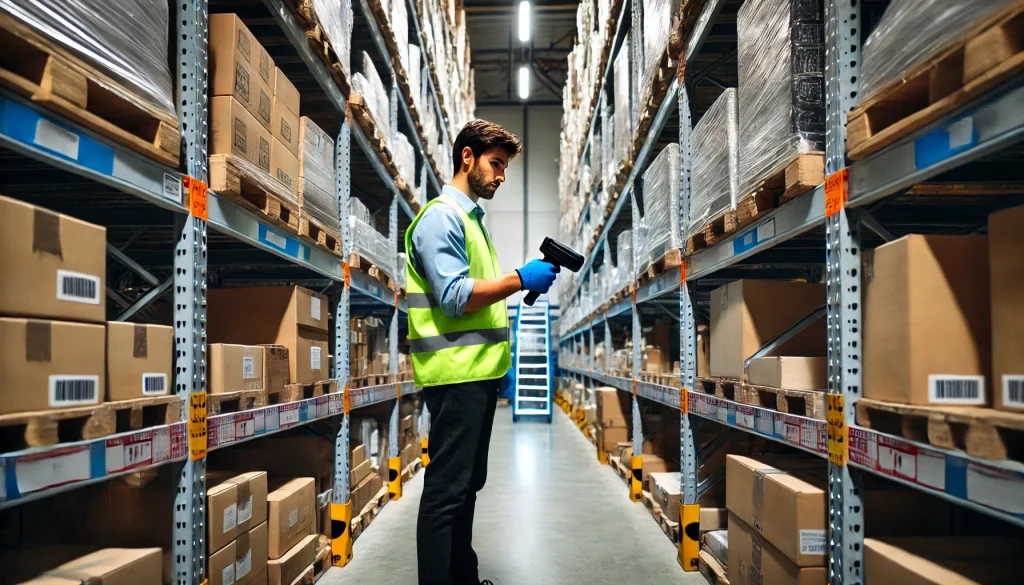
Regular Training
Continuous training ensures that warehouse staff are knowledgeable about the latest technologies and best practices. Regular training sessions help maintain high levels of efficiency and accuracy in the putaway process.
Efficient Layout Design
Designing an efficient warehouse layout facilitates smooth movement and optimal storage. Consider factors like item size, weight, and retrieval frequency when planning the layout.
Consistent Monitoring
Regularly monitor and assess putaway processes to identify and address inefficiencies. Use performance metrics and KPIs to track progress and make informed improvements.
Use of Technology
Leverage advanced technologies like WMS, RFID, and AGVs to enhance the accuracy and efficiency of the putaway process. Integrating these technologies can streamline operations and reduce manual errors.
Continuous Improvement
Regularly review and improve putaway processes to adapt to changing needs and enhance performance. Implement feedback loops and encourage staff to suggest improvements.
Metrics and KPIs
Tracking key performance indicators (KPIs) is crucial for evaluating and improving the putaway process.
Putaway Accuracy
Measures the correctness of items being placed in their designated locations. High accuracy is crucial for efficient inventory management.
Putaway Cycle Time
Tracks the time taken to complete the putaway process from receiving to storing. Shorter cycle times indicate higher efficiency.
Labor Utilization
Assesses the productivity and efficiency of the workforce involved in putaway. Optimal labor utilization ensures that resources are used effectively.
Space Utilization
Evaluates how effectively the available storage space is used. Higher space utilization indicates better storage management.
Inventory Turnover
Monitors the rate at which inventory is cycled through the warehouse. Higher turnover rates suggest efficient inventory management and demand fulfillment.
Impact on Overall Warehouse Efficiency
The effectiveness of the putaway process has a significant impact on the overall efficiency and performance of a warehouse.
Operational Efficiency
Streamlined putaway processes reduce operational delays and costs, leading to higher overall efficiency.
Inventory Management
Accurate putaway enhances inventory control and reduces discrepancies, improving overall inventory management.
Customer Satisfaction
Efficient putaway leads to faster order fulfillment and improved service levels, resulting in higher customer satisfaction.
Cost Reduction
Effective putaway minimizes labor costs, reduces damage, and optimizes space utilization, contributing to overall cost reduction.
Scalability
Well-managed putaway processes allow warehouses to scale operations smoothly to meet growing demands, supporting business growth and adaptability.
Conclusion
In conclusion, putaway is a fundamental aspect of warehouse management that significantly impacts efficiency, accuracy, and overall productivity. By understanding and implementing effective putaway strategies, leveraging advanced technologies, and adhering to best practices, warehouses can optimize their operations and achieve higher levels of efficiency and customer satisfaction.